Scientists have devised an approach for 3D printing metal, which has the potential to lower expenses and enhance the economical utilisation of resources
A research group led by the University of Cambridge has introduced a new technique enabling the incorporation of predetermined structural changes into metal alloys during 3D printing. This method refines their characteristics without relying on the traditional ‘heating and shaping’ process employed for millennia.
Innovative 3D printing
This 3D printing technique merges the desirable attributes from both realms: the intricate forms achievable through 3D printing and the capacity to manipulate the composition and attributes of metals, as facilitated by conventional approaches.
3D printing offers numerous benefits compared to alternative manufacturing techniques. For instance, it simplifies the production of intricate forms and requires significantly less material than conventional metal manufacturing methods, further enhancing efficiency.
“There’s a lot of promise around 3D printing, but it’s still not in wide use in industry, mostly because of high production costs,”
“One of the main drivers of these costs is the amount of tweaking that materials need after production.” said Dr Matteo Seita from Cambridge’s Department of Engineering, who led the research.
Comparing 3D printed steel to traditional methods
Since the Bronze Age, metal components have been created using a technique involving heating and forging. In this method, the material is strengthened through hammering and then made malleable by exposure to heat, enabling the craftsman to mould the metal into the desired configuration while imbuing it with specific physical characteristics like resilience and durability.
“The reason why heating and beating is so effective is because it changes the internal structure of the material, allowing control over its properties”
“That’s why it’s still in use after thousands of years.” said Seita.
A significant drawback of existing 3D printing methods is the inability to regulate the internal structure similarly, necessitating extensive post-production modifications.
Collaborating with colleagues from Singapore, Switzerland, Finland, and Australia, Seita has formulated a fresh formula for 3D-printed metal. This allows for precise management of the internal structure of the material while a laser is liquefying it.
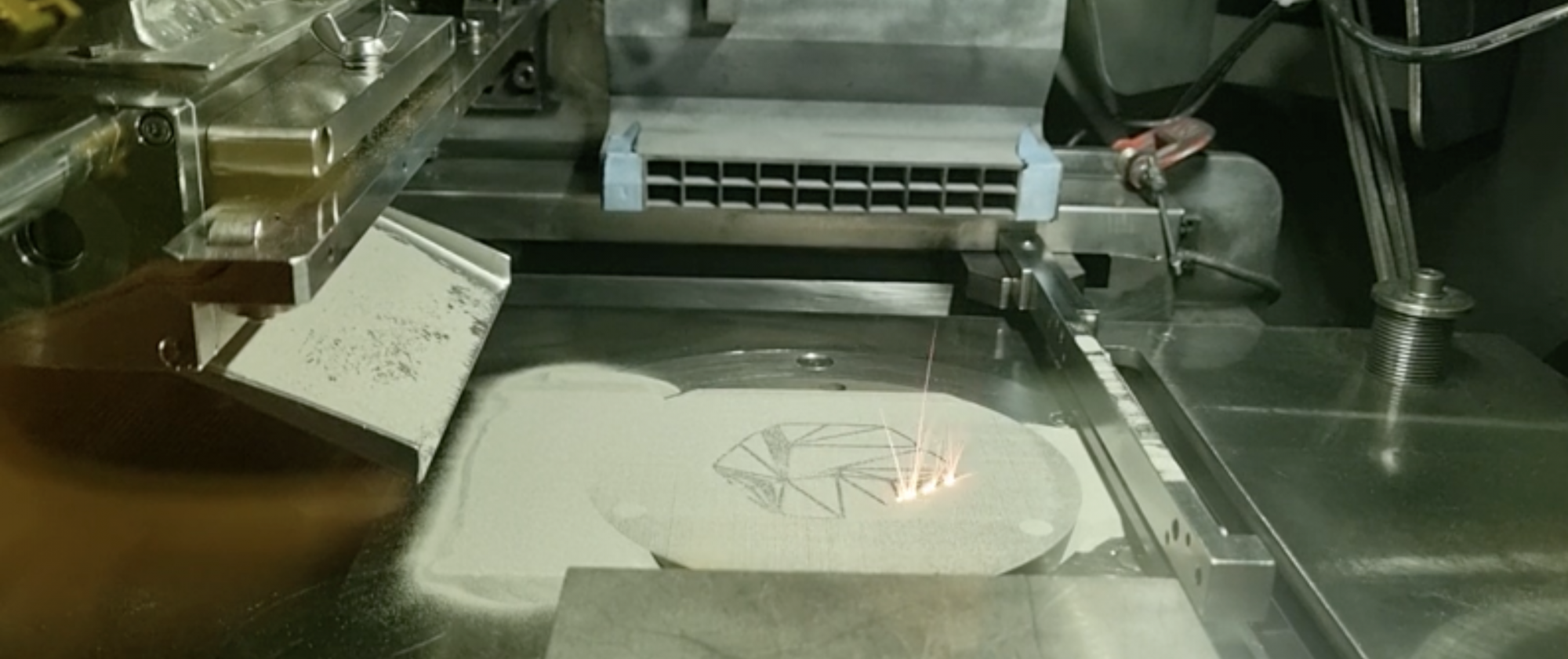
Achieving strength and toughness
By manipulating the material’s solidification process post-melting and regulating the heat generated during the procedure, the scientists can tailor the properties of the end product. Typically, metals are designed to be sturdy and resilient for safe usage in structural applications. Although 3D-printed metals possess inherent strength, they also exhibit brittleness.
The method devised by the researchers provides comprehensive control over strength and toughness. It accomplishes this by orchestrating a controlled reconfiguration of the microstructure when the 3D-printed metal component is subjected to relatively low-temperature treatment in a furnace. Their approach uses conventional laser-based 3D printing technologies with a minor adjustment to the process.
The 3D-printed steel they created, a product of theoretical design and experimental validation, comprises alternating segments of robust and durable material, delivering performance on par with steel crafted using the traditional method of heating and forging.