Researchers are working on a non-destructive method to measure strains, that can estimate the remaining lifecycle of mechanical products
Non-destructive inspections for cracks in turbine blades are periodically conducted in power generation plants. However, if the time between crack initiation and fracture is shorter than the inspection interval, there is a need to establish a non-destructive method to predict the remaining useful life even in absence of cracks.
Existing estimation methods aren’t accurate enough
Current methods for predicting remaining life include numerical analysis and measuring microscopic cracks and the surface hardness of turbines. However, many parameters are difficult to determine, such as the temperature distribution required for numerical analysis, and the estimation accuracy is relatively low. In addition, non-destructive methods can only measure a limited number of parts. Therefore, there is a need to establish a method for non-destructively evaluating the three-dimensional creep strain distribution.
After a relatively large earthquake, it is necessary to assess the damage quickly to decide whether the power plant can be restarted. Evaluation of plastic strain distribution is important in areas where there is a high possibility of damage. However, currently, only the surface of the components can be examined by hardness testing. Another problem is that the hardness tests are not non-destructive since they leave indentations. A relatively simple non-destructive evaluation of the plastic strain inside a piping system can quickly determine whether the plant can be restarted.
Three-dimensional creep strains and plastic strains could be the answer
Our research group is working on a technique to estimate three-dimensional creep strains and plastic strains using surface deformation and strains measured non-destructively. Since deformation is caused by inelastic strains, inelastic strains can be regarded as the cause and deformation as the result. Therefore, the process of determining inelastic strain from deformation in this study is an inverse problem.
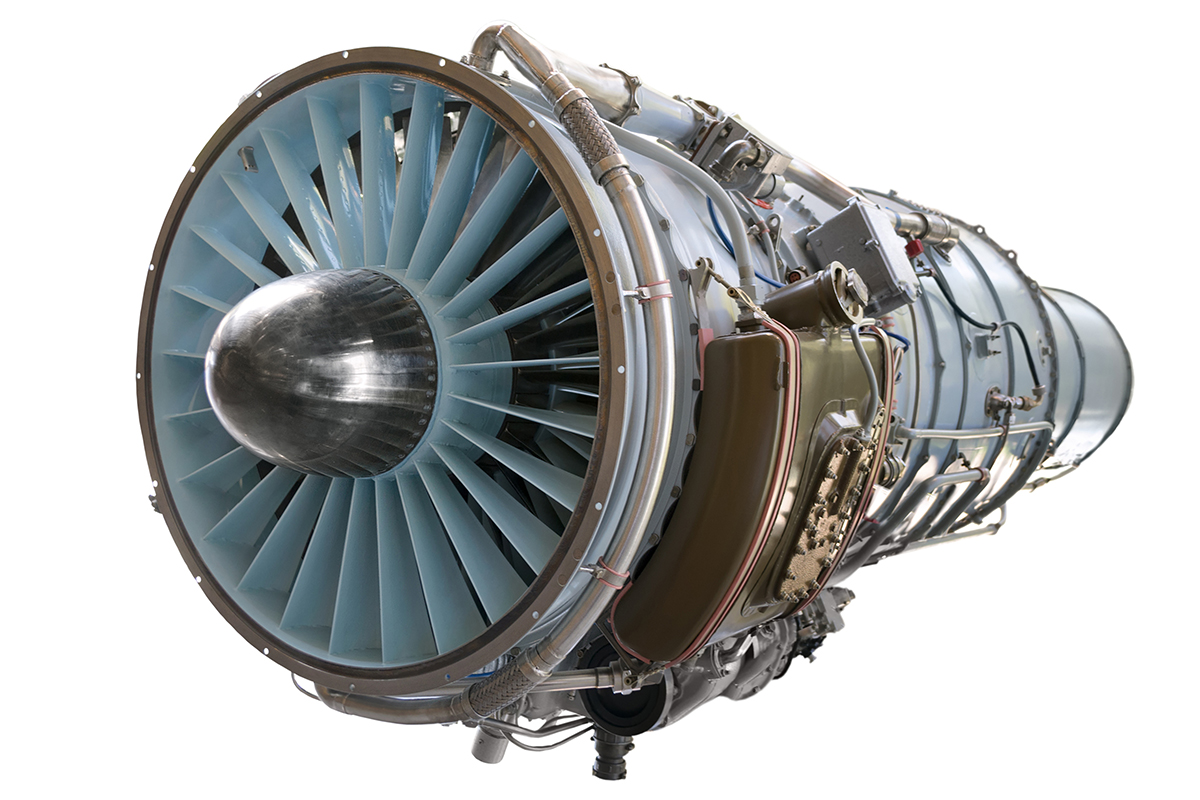
Revelations about the lifecycle of mechanical products
Two important results have been obtained from this research. First, in the case of turbine rotor blades, patterns applied to the surface disappear at high temperatures. Therefore, the deformation obtained is limited to certain points, such as corners. Second, the relationship between inelastic strain and deformation is non-linear.
The solution of these problems is expected to enable an approach to determine the internal inelastic strain from the surface deformation for all types of components. The method can be applied if the dimensions and material (Young’s modulus and Poisson’s ratio) of the component are known, even though the complex process of inelastic strain generation does not need to be known.
Please note: This is a commercial profile
© 2019. This work is licensed under CC-BY-NC-ND.