Dr Carlos Ziebert, leader of the group Batteries – Calorimetry and Safety, KIT, explains how electrochemical-calorimetric methods help to develop and safely upscale sodium-ion batteries
As part of the German Excellence Initiative, the KIT, the University of Ulm, the Center for Solar Energy and Hydrogen Research Baden-Württemberg, and the University of Giessen jointly launched 2019 the POLiS – Cluster of Excellence for Battery Research Post Lithium Storage, which is funded with 47 million euros over seven years to step away from the usual resources of Lithium, Nickel and Cobalt.
Sodium-ion batteries are better for the environment
Post-lithium batteries use more abundant and environmentally friendly materials, such as Sodium, Magnesium or Calcium. In the first 3.5-year funding period, the focus was laid on the development of sodium-ion batteries, which are based on the same working principle as a Lithium-ion battery. Instead of lithium ions, sodium-ions are transferred via an organic electrolyte through a separator between the two electrodes, in which they are intercalated and deintercalated, respectively.
Direct measurement of the heat flow during cycling by Tian-Calvet Calorimeter
The work in the group Batteries – Calorimetry and Safety at the KIT, IAM-AWP started with coin cells made of the commercial cathode material Na0.53MnO2 (NMO) and commercial coconut-shell-derived hard carbon (HC) as anode material. Besides the electrochemical, thermal characterization is needed to achieve an in-depth understanding of the underlying reaction mechanisms and heat conduction processes.
The MS80 Tian-Calvet calorimeter allows determining the total heat generation operando (while operating) during cycling with great accuracy by direct heat flow measurement. The heat flow is determined by the 3D Tian-Calvet Sensor arrangement, where both the sample and the reference vessel are surrounded by rings with hundreds of thermocouples. As shown in Fig. 1a), even if such cells have only a capacity of about 1 mAh the heat flow (green curve) can be clearly measured for the charge and discharge process as indicated by the applied current (red curve) and the resulting voltage (blue curve). For a charge/discharge rate of 0.2 C integration of the heat flow over time gives 1.3 J of generated heat during charging and 1.5 J during discharging.
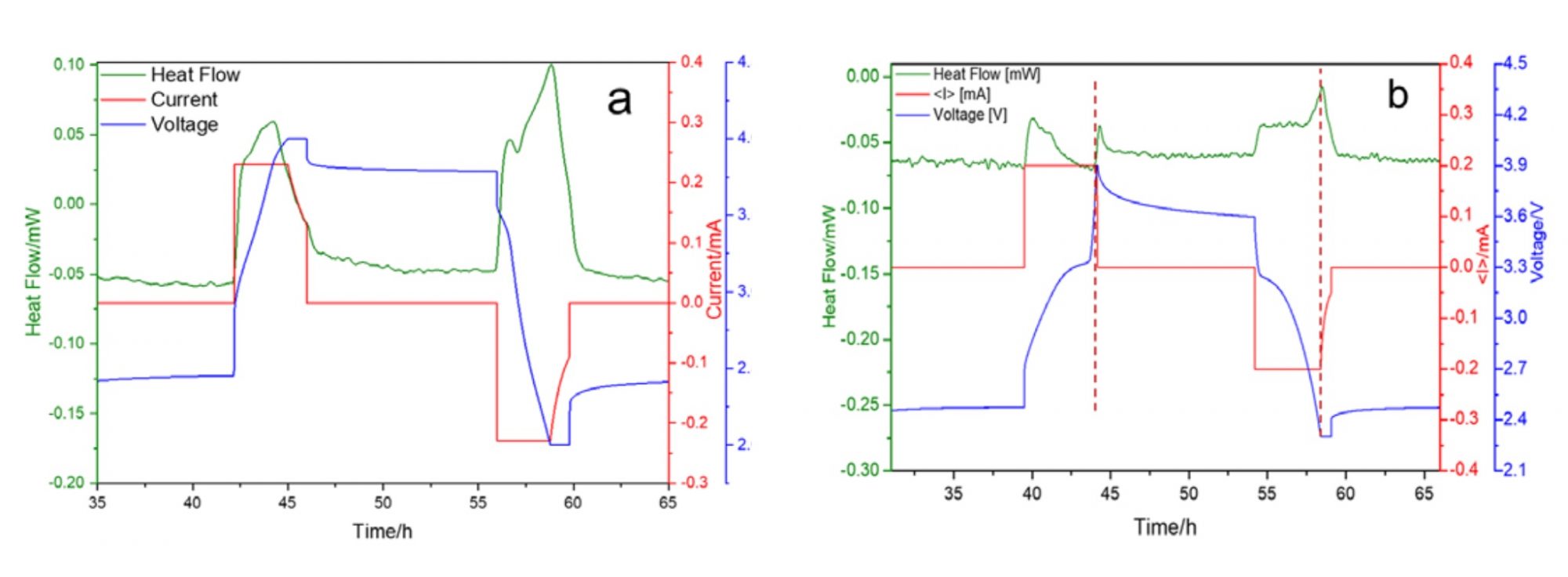
Enhancing the low intrinsic conductivity of NVP
The next step was to replace the NMO with porous Na3V2(PO4)3 (NVP) composites with carbon coating that have been developed at the Institute for Applied Materials – Energy Storage Systems (IAM-ESS) to enhance the low intrinsic conductivity of NVP by creating an electronic conductive network. Using this improved material, the heat generation of a coin cell was largely reduced by a factor of three, as can be seen in Fig. 1b). For a charge/discharge rate of 0.2 C the generated heat during charging was 0.3 J and during discharging it was 0.5 J. The further scale-up process to pouch cell level needs to be accompanied by safety tests (thermal abuse, overcharging, internal/external short circuit, mechanical impact) because safety concerns remain a critical barrier for the introduction of any post-lithium battery technology. Accelerating Rate Calorimeters (ARCs) are perfectly suited for these abuse tests. Fig. 2a) shows the temperature vs. time curve during a Heat-Wait-Seek (HWS) test on a stack of two NVP/C//HC coin cells with an electrolyte composition of 1 M NaClO4 in EC:DMC:EMC (1:1:1) plus 2% FEC.
The plateaus in the temperature curve indicate the different stages of the reactions that finally lead to the thermal runaway.
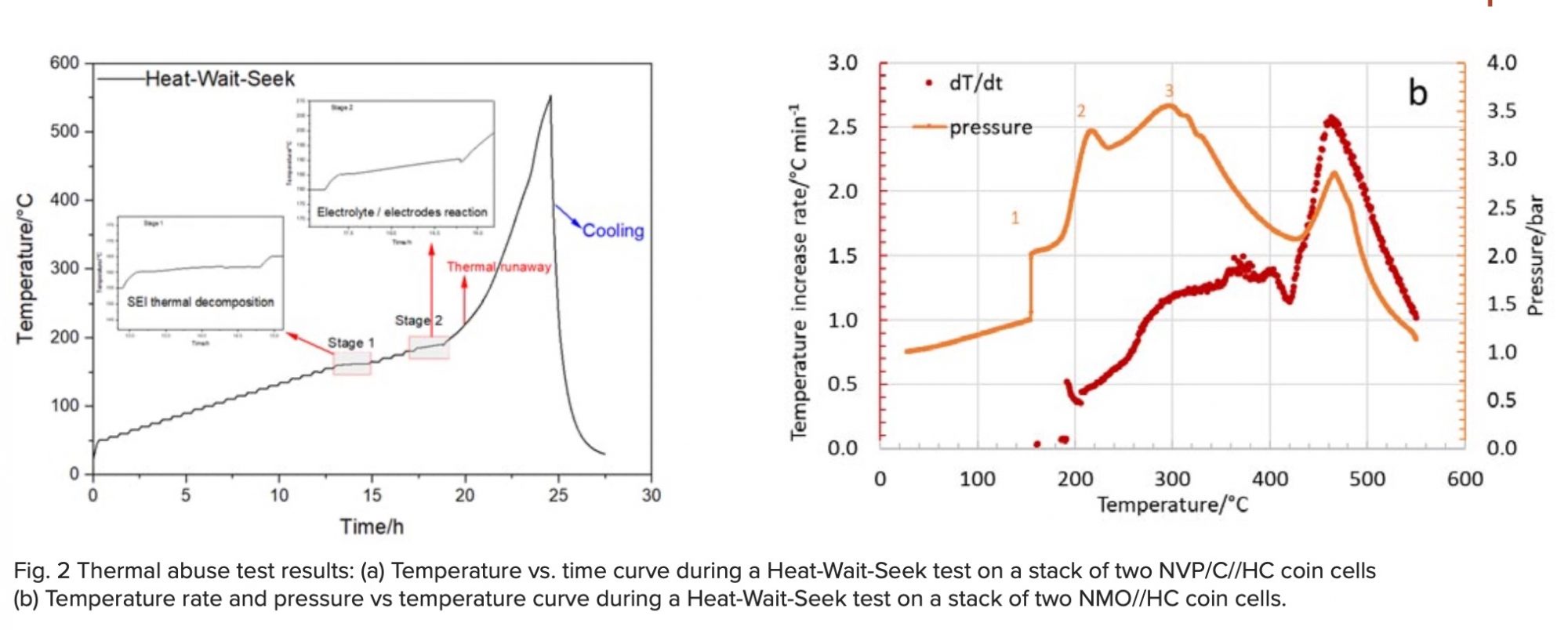
Calorimeters can pave the way for other post-lithium batteries
These can be seen more clearly in the two inserts. The first exothermic reaction represents the thermal decomposition of the solid-electrolyte interphase (SEI) layer. The second stage can be attributed to exothermic reactions between the electrolyte and anode, which is no longer protected by the SEI layer. The third stage is the thermal runaway, which starts at 200 °C and reaches a maximum of 550 °C, before the cell is cooled down by pressurized air. By using a closed cell holder, which has an opening to a capillary connected to a pressure transducer, the pressure increases by the gas that is formed during the different reactions can also be recorded, as demonstrated in Fig 2b), which shows the temperature rate (red circles) and the pressure (orange curve) both plotted against the temperature. The maximum values for the temperature rate and pressure were 1.5 °C/min and 3.5 bar, respectively. Recently the NVP/C-based cells have been successfully upscaled to 5 cm x 5 cm pouch cells, which reached a maximum capacity of 18 mAh and good cycling stability at C/5 charge/discharge rate with a remaining capacity of 88% after 300 cycles.
Thus, it has been demonstrated that the different types of calorimeters pave the way for mature and safe sodium-ion batteries and other post-lithium batteries.
https://www.postlithiumstorage.org/en/
This work contributes to the research performed at CELEST (Center for Electrochemical Energy Storage Ulm-Karlsruhe). This work was funded by the German Research Foundation (DFG) under Project ID 390874152 (POLiS Cluster of Excellence).

This work is licensed under Creative Commons Attribution-NonCommercial-NoDerivatives 4.0 International.