Open Access Government interviews Claus H. Ibsen, PhD, the Group R&D Director at Vestas aircoil A/S, and Professor Atul Bhaskar from the University of Sheffield on composite covers, ceramic 3D printing, and more, in their experimentation to make their products more sustainable
1. What recycled materials do you plan to use in the future and why?
We plan to use two types of materials – first, from various plant sources and the other, ceramics. This is because there are many kinds of ceramic and plantbased materials that have the potential of being used within load bearing parts. An obvious benefit of using plant fibres is that they are sustainable. While being good to recycle as in case of plant-based textiles, they are also easy to dispose of because of their biodegradability.
Additionally, with the fibres we are considering, a host of these plant materials have been experimented with for various applications before. Plant materials such as flax, cotton, recycled bamboo, jute, coir, and sisal, and so on, are all fibrous materials. The fibre architecture means that they are very strong. Many artificial structural composite materials use a fibre structure as well for similar reasons. Several strong and stiff composites used in aeronautical construction frequently use either glass or more often, carbon fibres. Both synthetic composites as well as natural composites exploit the strength along fibres.
A material like cotton used for textiles requires investment of a lot of energy, and it takes work to bring it to a woven form in which it gives best performance. What we are considering is recycling material that is already woven, as in, textiles that we wear. We use it, we throw away, and if we want to recycle it by making fibres again, there’s a lot of investment of energy back in. So, we had the idea of using it as it is in the woven form by making structural composites with recycled textiles. It has its challenges because every piece is different, making it hard to fabricate structures with consistent material properties. but how could we get a quantitative bound on what properties will derive out of those? Clays versus plant-based materials: which will stand the test of time?
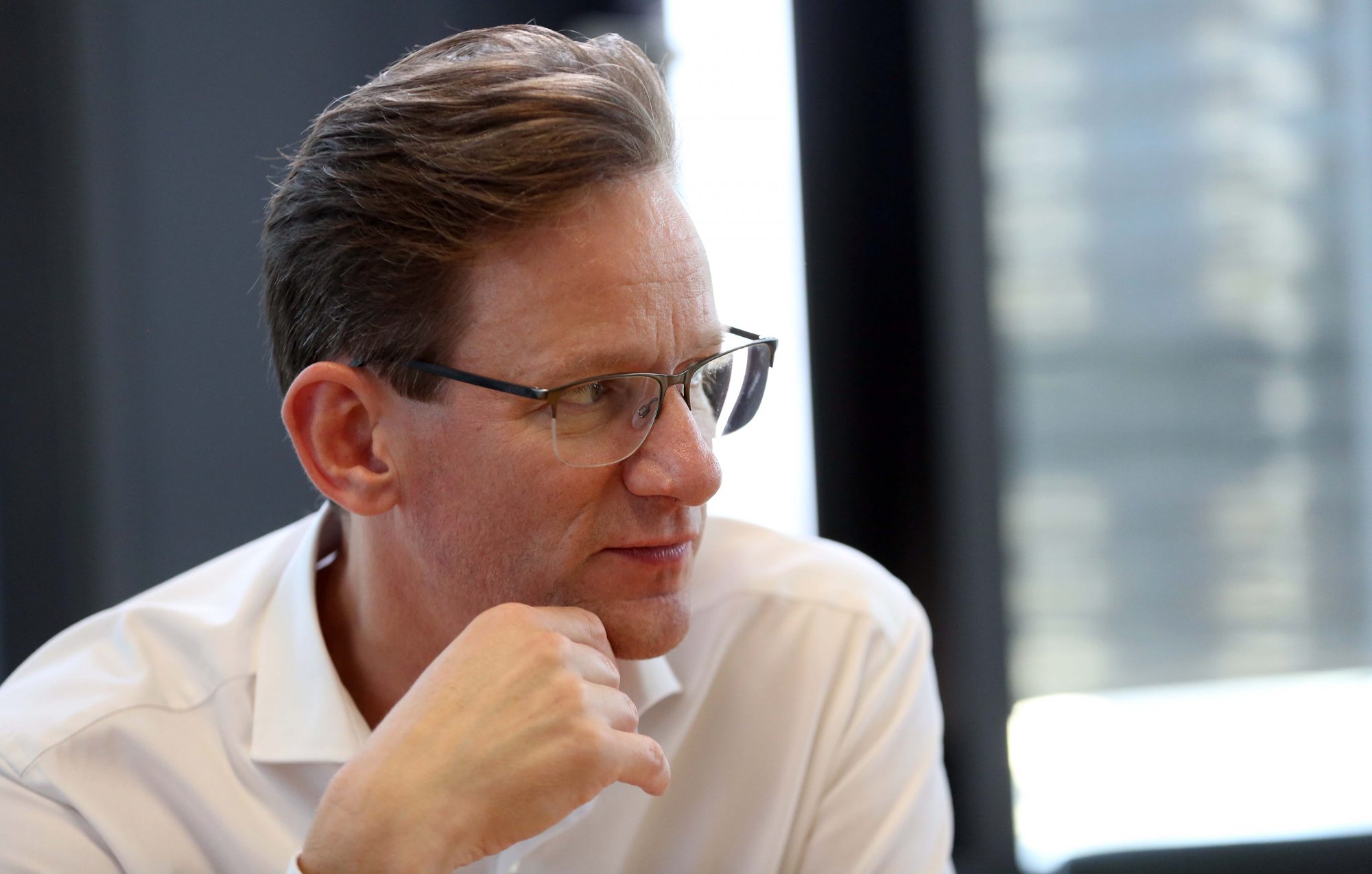
We are also considering using clays, as they are also environmentally friendly in many ways. While energy input is required to give shape and form starting from clay, it has an excellent afterlife. It’s much easier to dispose off also and doesn’t leave any adverse material trace to the environment when it degrades with time. In the case of clay-based structures, however, after the greens are made, one must fire it in a kiln or a furnace. While every material has strengths and weaknesses concerning it functional aspects, most ceramics are quite stiff structurally, but brittle – which means they are not good against any impact. Optimising mechanical stiffness and strength is a challenge; this is why we have taken up this research at the interface of manufacturing, strength of materials and mechanics.
There are complementary properties in different materials, for example, that clays are excellent against high temperature, whereas plant-based fibres are not. So, we have two sides of research which we can explore, and that’s where we ought to carry out a comparative study when it comes to decision making concerning the best technology for an engineering challenge that involves competing requirement. Bamboo is another incredibly interesting material. It is used in Southeast Asia in the construction industry, especially for scaffolds.
It has a hierarchical structure. Its knots and hollows give it a very interesting mechanical property, but more importantly, it has fibres running in it providing excellent strength and stiffness along their main direction. One good thing with bamboo is that when it fractures, it doesn’t break apart. So, it has a lot of residual strength in it because of the fibre. Its fibrous architecture makes it a very interesting and versatile natural material. The overall environmental impact invariably requires a life cycle analysis.
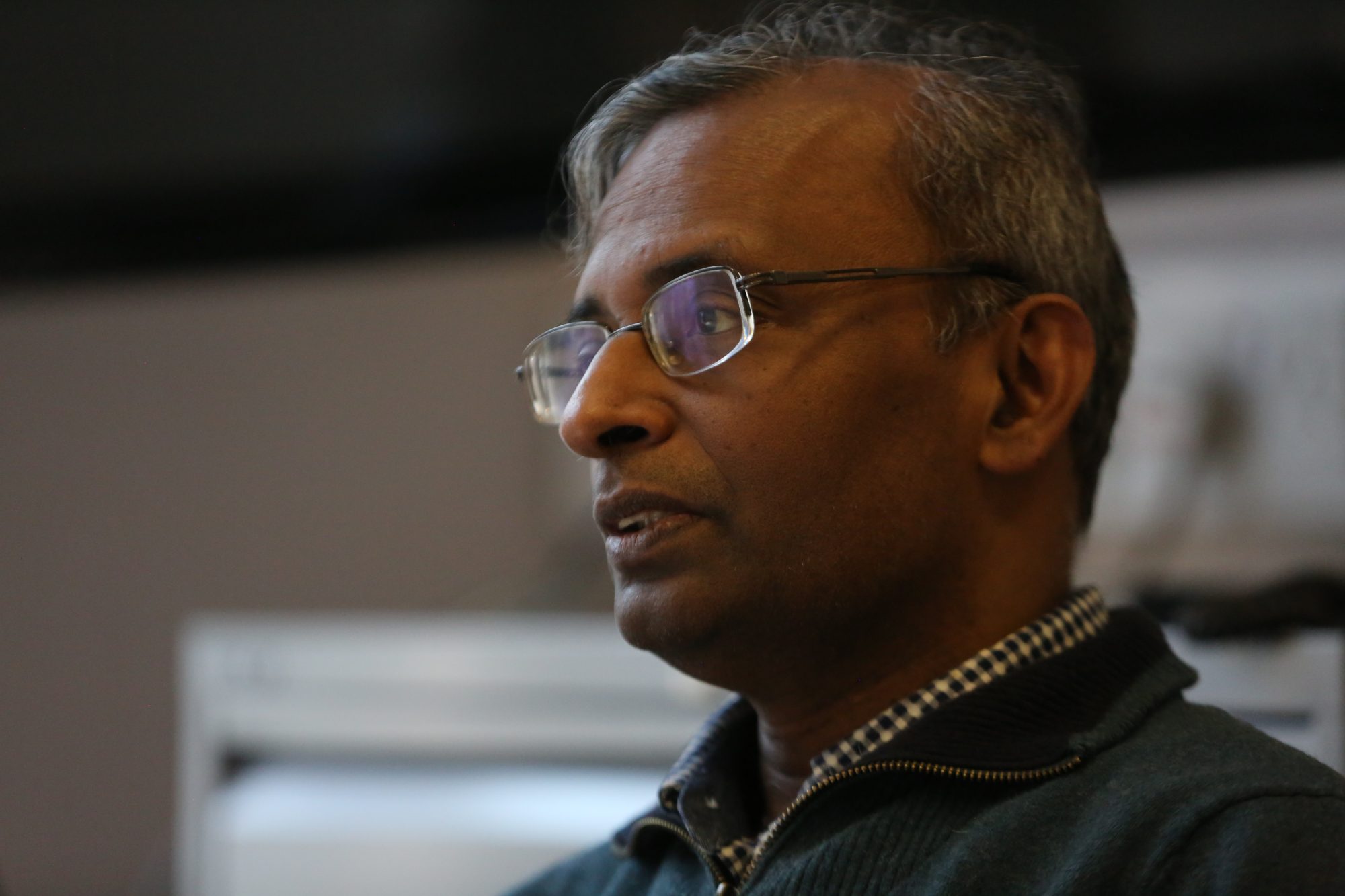
2. How are the cover structures tested in your work?
Our current technique for strength evaluation is destructive testing: we produce specimens first, and then test them and check at what loading they fail. It’s a challenging to make reliable digital models for predicting the strength of these structures because their internal structure is not uniform. While models for structural and material stiffness are usually reliable, those for strength are relatively less so and therefore structural testing in inevitable. The material heterogeneity poses additional challenges to computational modelling. We plan to take this variability into account and also estimate bounds on the properties that is useable within a design framework.
The use of multiscale modelling in engineering The internal architecture of the material is multi-scale, with fibres that are embedded within a matrix. This gives us opportunities for novel research in the area of multiscale modelling. We will test our materials in a normal way to begin with, where we make samples and use tensile testing machines. The structure is expected to be loaded under pressure, which means we also plan to do some tests in which the bending stiffness and strength will be assessed. While we don’t have a final design currently, as this would develop during the project, we have preliminary ideas about geometry, material and target functions of the product. There are opportunities for optimisation of both material and structural design. Appropriate safety margins will need to be incorporated into the design, so that the product could pass certification.
3. Describe your planned processes with ceramic printing
There are two common additive manufacturing processes relevant to printing with ceramics. One of these makes use of material in the powder form as the starting point. In this process, one has a bed of powder of the material dispensed first. A computer-controlled nozzle then runs in a predetermined path in the plane. Through the nozzle, one essentially dispenses some liquid, a binder. In some cases, the binder could be as simple as water. For example, plaster of Paris printing would generally start with a layer of powder material, with water binding it. Then, due to an exothermic reaction, the powder would bind. Or if you have a clay, the clay will produce a green which will have to be taken to a furnace or kiln and fired so that it hardens. Fused deposition modelling (FDM) is mostly used for polymers, where you have a molten material that is extruded. The second class of ceramic 3D printers make use of extrusion.
While the material is dispensed using a technology very similar to FDM, i.e., using computer control, where a slicing software does a very similar job – it further instructs the machine as to how the dispenser must move in the XY plane. Through the nozzle, a slurry or paste of the ceramic material, say clay, is extruded under pressure so that the nozzle can run in a plane in a predetermined manner. After completing one layer, one goes to the next layer and the next layer and so on. Each layer can be different, and it is programmed like in any fused deposition modelling process. That’s where the similarity with FDM stops. The printed part is called a ceramic green. Like a potter’s creation, one takes it to a kiln or a furnace next to complete the process.
During this process, dimensional changes take place – which is where a lot of unknown science currently rests. The benefit of both types of additive manufacturing with ceramics is the excellent dimensional control, in addition to the flexibility of fabricating complex shapes. Hygromechanics and dimensional changes in the material The material can shrink or undergo dimensional changes after the additive manufacturing of ceramic greens. Predictive modelling of this will be informed by experiments. While moisture is lost in the furnace, the material becomes stiffer and stronger, but it also changes its size. We need to know this precisely to ensure that nuts, bolts, screws, etc., fit properly.
With the use of natural materials, there is also the issue of dimensional changes due to moisture, but in the opposite direction. Moisture can be lost in service from plant-based composites, while using plant based material at high temperatures. We need to quantify this accurately.
In the case of ceramics like clay, moisture losses usually occur at the time of manufacture rather than service. In the case of plant-based composite, it’s during service. The physics of swelling and shrinking due to moisture is known as ‘hygromechanics’. Interestingly, very little is known about hygromechanics.
How material expands or shrinks due to the loss or gain of moisture is very poorly understood. It does the same thing as producing some strain – everything shrinks or expands slightly, but that slight expansion or shrinkage could be bad enough so that you’ve created a pot and it doesn’t fit. Therefore, it is vital that we characterise the dimensional changes as part of our planned project.
4. What are the challenges in manufacturing?
While fabricating larger components, such as those that are two metres long and one metre high, there can be a bit of a challenge, especially regarding the shrinking and how to control that. We will start to experiment with small specimen, both in the laboratory and computationally. Guided by this experience, we plan to scale up the manufacturing to a larger component.
When it comes to nozzle-based extrusion, the nozzle diameter determines the resolution of printing, and the nozzle diameter is closely related. The smallest nozzle diameter is closely related to the particle size in the ceramic slurry. The use of a small diameter nozzle during 3D printing results is good resolution, but it is accompanied by poor manufacturing speed – so there is a trade-off between printing speed and the resolution.
We are considering either repurposing existing printers or using those with multiple nozzles, where certain parts could be quickly manufactured using a large diameter nozzle, with large particle size quickly, and where one needs to fill an area quickly, where coarse resolution is acceptable. Fine resolution could be achieved during 3D printing using small diameter nozzles in regions where this is required, thus optimising fabrication time and resolution simultaneously.
5. How can this be combined with topology optimization and better vibration damping?
Exploring materials with low Q factor for vibrational damping
Metals are excellent regarding formability, machinability, stiffness, strength, and so on, but structures made of metals are lightly damped against vibration. Damping is a material property – the less damped a material, the structure rings longer upon being mechanically excited. Added to this, the use of metals goes well with the use of traditional workshops. By contrast, plant-based materials as well as ceramics can potentially be damped. Therefore, the use of materials such as ceramics and green composites offer an opportunity to achieve vibration damping.
On the other hand, manufacturing over the last 200 years has developed with tools that are suitable for manufacturing with metals. However, manufacturing is currently undergoing a major transformation because of the digital revolution, and materials that should have been used, in my view, were not used primarily because of the tools or because of the processes Q factor is a measure of material damping.
A high Q factor means low damping, and a low Q factor means high damping. We conjecture that material based on natural fibres and their composites are likely to be high damping, low Q compared to metals. This can be intuitively understood as metals ring when struck mechanically The Q factor of ceramics is expected to be in between the metals and the natural composites. Since we have a spectrum of material to work with, we might even want to combine good parts of different materials together in the material usage.
Shape and topology optimisation
Topology optimisation is frequently carried out using a digital mechanical model of a component. Within the project, we will explore ways to optimise the structure for low cost and weight while ensuring structural stiffness and integrity by making use of shape and topology optimisation to enhance the structural performance. While carrying out structural design using computational tools, the aim is to give shape and size to a structure that performs a certain function – the function of this part is to bear the load. The challenge here is to use these techniques while using recyclable material is from plant origin or clay.
Additive manufacturing provides additional freedom to the design engineer, as complex geometries could be fabricated now that was not possible before. This brings us to complex topologies. Complex topologies have not been tried for such applications before, mostly because manufacturing costs are too high for unusual topologies and shapes when using conventional subtractive manufacturing. While using 3D printers, the degree of difficulty in manufacturing is often the same regardless of the complexity of the geometry of the part being fabricated. This opens up new opportunities for fabricating novel structures. An interesting possibility includes cellular architectures in conjunction with ribs to optimise stiffness, and so on.
Similar promising structures, such as sandwich constructions, are frequently used in the aeronautical industry, where manufacturing cost is less important. The novel manufacturing is now affordable, and many structural ideas can be translated to other sectors of industry where attempting complex geometry was previously prohibitive because of the manufacturing costs. To summarise, we are excited to get started. This is one of the most interesting projects that we have initiated in a long time. We have hit a sweet spot here with the timing also.
Exploring the Tersus cooler cleaning system: A model of sustainability
For Vestas Aircoil, research is all about contributing to sustainability in an industry that for the most part is considered anything but sustainable in its origin. Project Manager Jens Meyer Olesen and Area Sales Manager Peter Jørgensen are heavily involved in the Tersus project at Vestas aircoil, which to them, is a winwin situation for sustainability. Jens Meyer Olesen comes from a background as a shipbuilder, Navy officer, and mechanical engineer. Peter Jørgensen has a background as a mechanical engineer and 25 years in the energy industry.
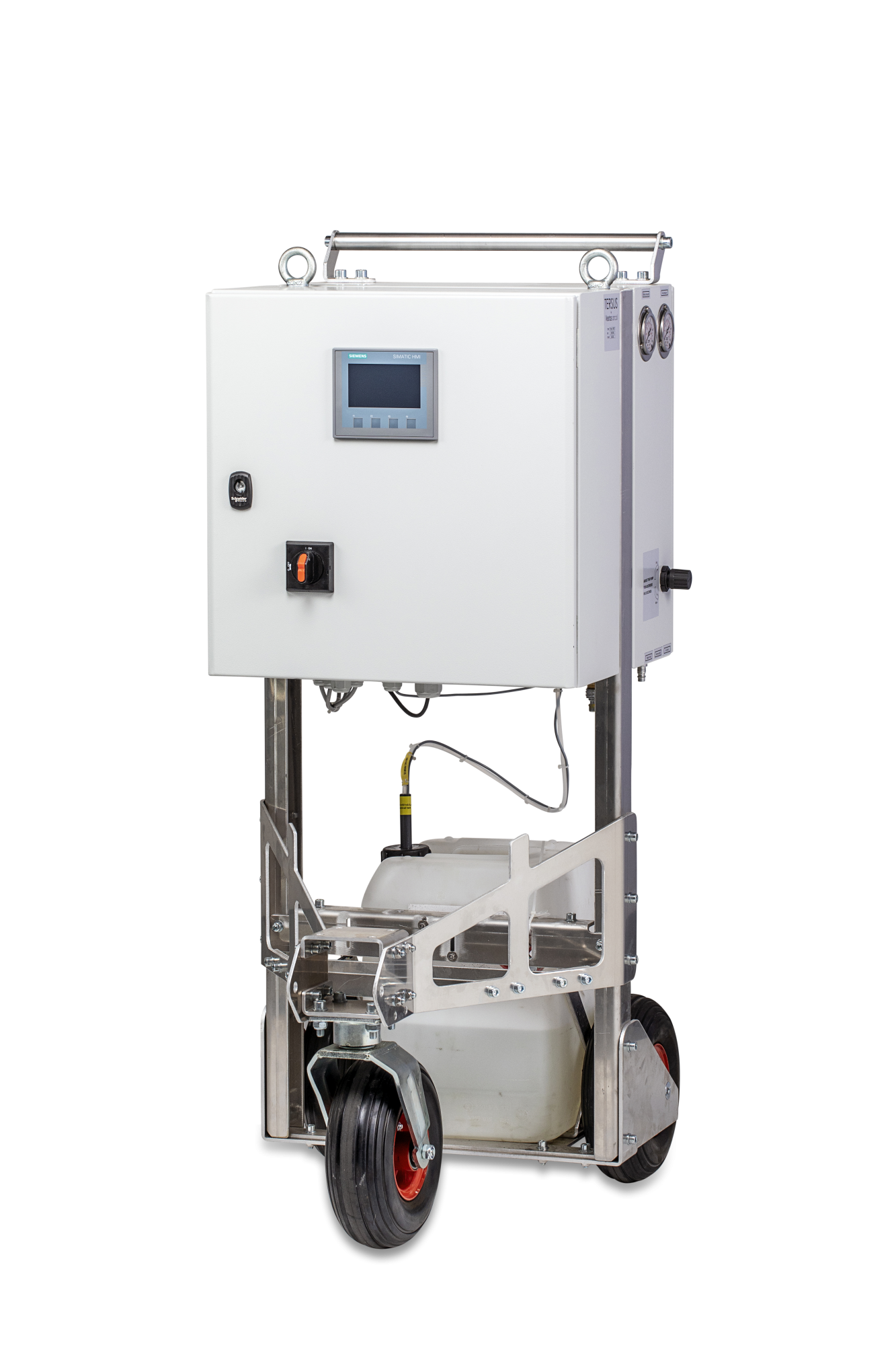
system
They are both highly motivated to make a difference for the environment and create solutions that make us work smarter instead of harder. “In my work, I have always looked towards offering new and innovative solutions that reduce the CO2 emissions while being financially beneficial for customers”, Peter Jørgensen explains. “I’m always looking for a win-win situation. All contributions to a sustainable world, large and small, will make the difference for the environment we desperately need”.
‘Radical solutions that improve our life and industry’ Coming from the marine and steel industry working at Lindø Shipyard, project manager Jens Meyer Olesen wants to make a difference in this industry. “I know which challenges we’re facing from the inside perspective, and I’m driven by a desire to create solutions that radically improve everyday challenges for the benefit of the environment”. Both Jens and Peter’s ambitions converge in the Tersus project. It is part of an initiative that can lead us to a more sustainable solution in an industry whose origin is anything but sustainable.
The Tersus cooler cleaning system is a unique solution that optimizes cooler performance in large engines. We have developed it to be user-friendly, safe and cost-effective. The task is to ensure that the cooler performance continuously stays at the highest possible level.
Cleaning reduces fuel consumption
Cleaning the cooler of an engine is essential to reduce fuel consumption and the engine’s downtime. The Tersus system is a compact and mobile cleaning system that is easy to operate and connect and can be used for most engines. Cleaning can be done on-site, making it more likely to be done more frequently, and this is a very efficient way of cleaning the air cooler. With our Tersus solution installed, cleaning becomes even more straightforward as you do not have to remove the cooler from the engine.
How does the cleaning unit work?
The Tersus cooler cleaning unit generates a foam with a unique physical and chemical composition. Once the foam is injected into the cooler and reacts with the dirt accumulated on the fins, it collapses into a liquid form, which can be drained quickly. By simplifying the cleaning process, you do not need to remove or transport the cooler, so the risk of damaging the cooler during transport is removed. As the cleaning process is likely to be performed more frequently, the cooler’s life span will increase and keep the differential pressure at an optimal level. An optimal differential pressure will lead to consistent fuel consumption.
The benefits of the Tersus cooling system are limitless
- Environment: Reduced fuel consumption as the cooler maintenance optimizes performance. No packing or transportation to the service facility for cleaning is required.
- Safety: No cooler damage during hoisting operation, as the cooler remains attached to the engine. This includes a limited risk of contact with contaminated cleaning agents. • Lower OPEX: Regular cleaning of the coil will increase fuel efficiency and the lifetime of the cooler.
- Reduced downtime: Easy to schedule downtime due to an efficient cleaning process and reduce man-hours and labour costs.
What are the ambitions for the future?
With Tersus, the cleaning process is highly automated, and we plan to keep maturing, improving, and updating the software for better and more user-friendly performance. This is done in close collaboration with our customers. We must get the Tersus cooler cleaning system out to as many as possible to improve fuel efficiency, extend the lifetime and reduce fuel consumption. We see Tersus as part of a transition into a greener future for everyone.
What do the customers say about the cooler?
We have had positive feedback from our customers. They are willing to try the unit and help us with feedback to keep things moving forward. We are very grateful for this collaboration that takes computer simulations into the physical world, working with the people using our equipment. This will only help to improve our work and reach our ambitious goals.
Sustainability in the research of digital twin technology
The performance of engines has a significant impact on the environment, particularly in terms of emissions and fuel consumption. As the world becomes increasingly aware of the consequences of climate change, there is a growing need for a green transition towards a more sustainable future. One critical aspect of achieving this transition is the optimization of engine performance to minimize fuel consumption and emissions while maximizing efficiency. Optimizing engine performance can lead to significant environmental benefits.
By reducing fuel consumption, we can reduce carbon emissions, which contribute to global warming and climate change. Additionally, optimizing engine performance can reduce other harmful emissions, such as nitrogen oxide, particulate matter, and sulphur dioxide, which can have negative impacts on human health and the environment. Furthermore, improving engine performance can increase the lifespan of the engine and reduce the need for replacement, minimizing waste and contributing to a more sustainable future. One way to improve the engine performance is to optimize the cooler of the engine system.
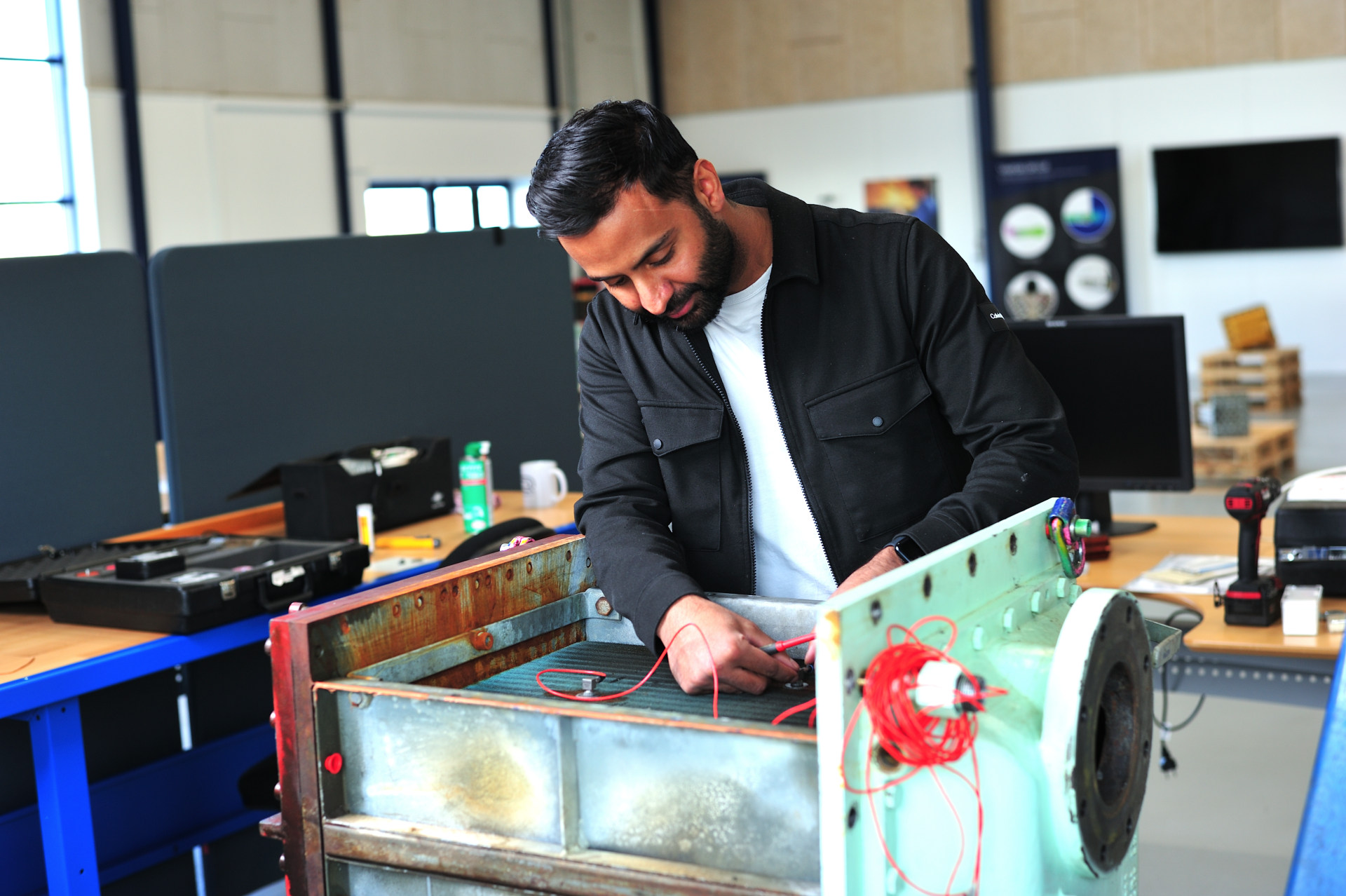
The cooler plays a vital role in the cooling system of the engine which is responsible for generating the power that propels the vessel. An inefficient cooler can cause the engine to overheat, leading to reduced performance and higher fuel consumption. Conversely, a properly designed and optimized cooler can potentially reduce the engine’s energy consumption, leading to lower fuel costs and emissions. We at Vestas Aircoil follow the pathway of digitalization and strive towards using sophisticated IoT and digital twin solutions to optimize our coolers in favour of maximising engine efficiency and becoming a player in the green transition.
What is a digital twin?
A digital twin is a virtual representation of a physical system that serves as the real-time digital surrogate, which provides an indication of its engineering performance. Data is sent to the digital model from the physical product, with the purpose of the digital model being able to provide performance measures to optimize the product. A digital twin is necessarily a multi-disciplinary concept, where well-trained scientists would integrate technology to provide indicators of engineering performance.
InDEStruct provided such a platform, showcasing that this non-trivial challenge can be solved in an elegant and efficient manner. Digitalization of physical assets (the physical structure/component of interest) is becoming more prominent in the engineering industry due to intelligent knowledge transfer through data.
The utilisation of advanced data analytics and sophisticated IoT technology to optimize the asset is now used in a digital twin context. This involves a well-formalized mathematical model (digital twin) that mirrors subcomponents of an assembled structure and is continuously updated by real-time data. Digital twins save on production costs and testing from an industrial perspective, a digital twin has the potential to generate new revenue streams and provide cost savings by minimising expensive laboratory testing, hence delivering growth with increased insight and real-time data.
As an example, the use of digital twins originates from NASA under the Apollo 13 mission in 1970 where two space aircrafts were built. One of the aircrafts (the twin) was left on Earth to reflect the realtime condition of the operational aircraft in space. The twin was used for training purposes and was consistently updated with multiple real-time data inputs from the operational aircraft in order to mirror a “realistic” space scenario. This exemplifies that a robust digital twin concept is not derived from one source of data but from multiple sources that maps real-time data to the replica structure, namely, the twin for enhanced performance.
Technology with real-time information
Vestas aircoil A/S has acknowledged the use of such intelligent systems for many years. In the Horizon 2020 InDEStruct Vestas aircoil A/S partnered up with the University of Southampton and the project was a strong asset in this regard. The platform of integrating a multi-disciplinary digital twin concept with well-trained scientists to integrate a technology which provides realtime information on structural performance was fully in compliance with the inDEStruct project.
The ambition of the project was to train a new generation of creative, entrepreneurial & innovative early-stage researchers (ESRs) with a focus on intensive doctoral training and to provide enhanced career perspectives in both the academic and non-academic sectors through intersectoral mobility. More specifically, the outcome of the project initiated new knowledge and methods of our heat exchangers in the form of:
- Experimental and operational modal analysis to investigate the vibration characteristics of components and assemblies under in-situ and laboratory testing
- The availability of truncated digital models through a developed Graphical User Interface (GUI) which is capable of computing the modal parameters of tubefin assemblies
- A method for fatigue life estimation via frequency (or temporal) based response functions obtained through the digital model. The project composition of academic and non-academic partners is of great importance to European research within mechanical and materials engineering with direct implications for the industry of heat exchangers, air cooling and exhaust gas systems. This work will also be of great interest to overseas companies and research communities, thus improving European competitiveness.
Vestas Aircoil A/S is currently engaged in a new project. It aims at developing cost-effective digital twin frameworks based on digital sensing units. Large costs associated with digital twin technology is blocking the road of a digital transformation for SMEs within the machinery and construction sectors.
This roadblock will be addressed by state-of-the-art sensing technology, computing technology, simulation acceleration and co-simulation-based digital twins provided by a project consortium consisting of industrial partners and academic partners.
Multisectoral applicability of digital twins
The intensive commitment within the area of digital twins, with a particular focus on the multisectoral applicability of a sophisticated digital twin, has led Vestas aircoil A/S to the next step in the journey of digitalization.
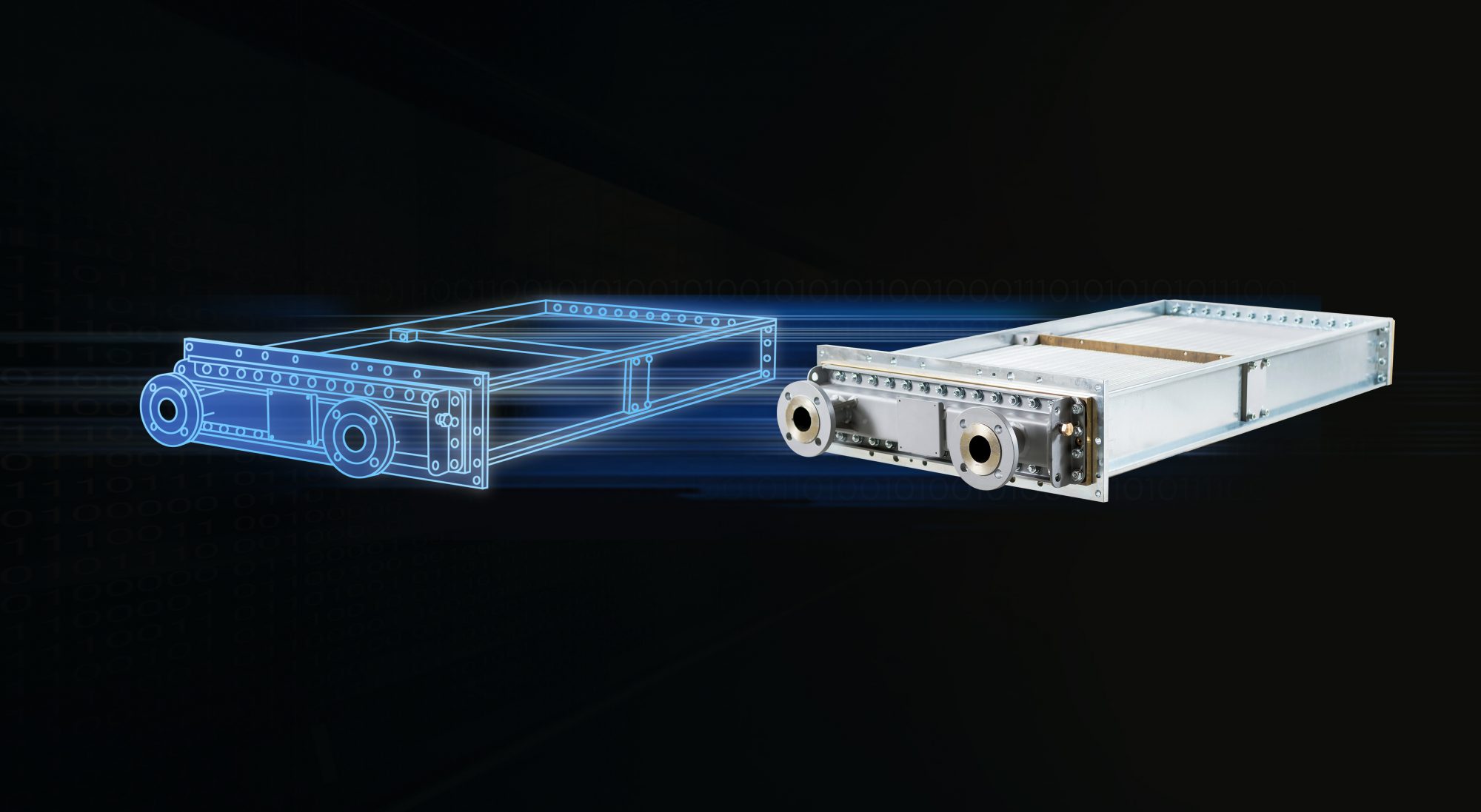
The goal and ambition are to carry out state-of-the-art industrial research in collaboration with academia towards realising the use of high-fidelity models and multi-structured data sources of our charge air coolers and heat exchangers. All this is in favour of optimizing design modification, predictive maintenance, real-time monitoring, and fault detection.
One of our active and ongoing projects is in collaboration with Alfa Laval and FORCE Technology with support from Hottinger Brüel and Kjær, Aalborg University Esbjerg, and the University of Southern Denmark that will, in a combined fashion, realise a digital twin of a charge air cooler on a selected engine. This project will focus on strengthening the research and industrial community, providing project proposals for the students in different universities, networking & collaboration between academia and industry and, finally, providing upfront research within the area of the digital twin concept.
Overall, digital twin technology can play a crucial role in optimizing charge air coolers and heat exchangers for, among others, the marine industry, ultimately leading to a more sustainable future. As mentioned in the paper on the journey to digitalization with the digital twin concept, digital twins are mathematical models that mimic the physical structure of an object and can be continuously updated with real-time data.
By using such a digital twin, we can accurately predict its performance under different operational conditions, and then use the data to make improvements that increase efficiency and reduce waste. Furthermore, such optimization can also reduce fuel consumption and emissions in marine vessels. Not only does the technology has its merits in engine efficiency but also identifies areas for improvement.
Modelling and predicting the flow of fluid through the cooler
One example of how digital twin technology can help optimize coolers is by simulating the fluid dynamics of the cooling system. A digital twin can accurately model the flow of fluid through the cooler, allowing us to identify areas of turbulence and resistance that can cause inefficiencies.
By making small modifications to the design of the cooler based on the insights gained from the digital twin, we can reduce turbulence and resistance, leading to a more efficient cooling system. Such type of analysis can be performed much faster and more cost-effectively than traditional physical testing methods and potentially culminates in reducing the time and cost required to bring a new cooler to the market.
In addition to reducing fuel consumption and emissions, optimized coolers can also lead to longer engine lifetimes and contribute to a more sustainable green future. By accurately predicting the performance of a cooler using a digital twin, we can identify potential areas of failure and develop maintenance plans that proactively address issues before they lead to engine downtime or failure. This can extend the life of the engine, reducing waste and minimizing the need for the replacement of parts or entire units of the engine system.
In conclusion, by incorporating digital twin technology into our design and testing processes, we can make significant strides towards a more sustainable future in the marine industry. This technology allows us to optimize the performance of our coolers, reducing fuel consumption and emissions while extending engine lifetimes and reducing waste.
Additionally, digital twin technology allows for faster and more cost-effective testing and design optimization that leads to more efficient products and lower environmental impacts. As a company, we are committed to utilizing advanced technologies like digital twins to help create a more sustainable future for all.
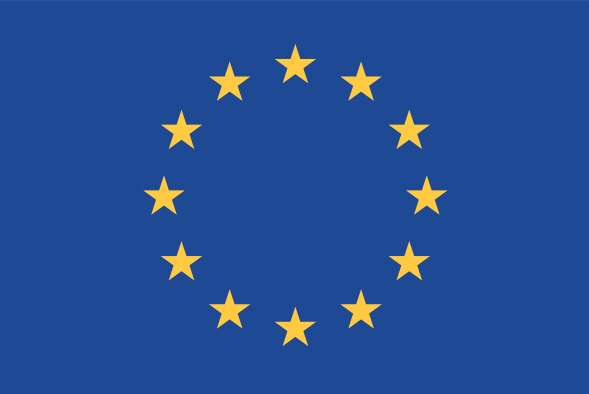
funding from the European Union’s
HORIZON 2020 research and
innovation programme under the
Grant Agreement no. 765636.