Uncured carbon fibre recycling by Bulk Moulding Compound (BMC)
Another route to valorise the fresh carbon prepreg scrap from aeronautical field has been stablished by Gaiker in MC4. In this case the scrap is used to develop bulk moulding compound (BMC), an intermediate product relying on short fibre, for production of new composite for transport applications. This new approach permits valorise a wide range of fresh prepreg scrap without any dimensional restrictions. This scrap is ground to reduce the fibre length and manufacture a BMC material mixing with new virgin resin formulation.
An appropriate virgin resin formulation should be defined based on properties of scrap to ensure the compatibility between scrap and virgin material. The BMC produced is transformed to final composite part by a moulding process where temperature, pressure and time should be stablished to ensure the polymerization of material as well as correct geometry qualities and tolerances. Regarding the properties of this new composite, the initial studies reveal that the mechanical performance of the composite produced with new BMC is equivalent to commercial BMC based on virgin raw materials, with more than 250 MPa of flexural strength and more than 80 MPa of tensile strength.
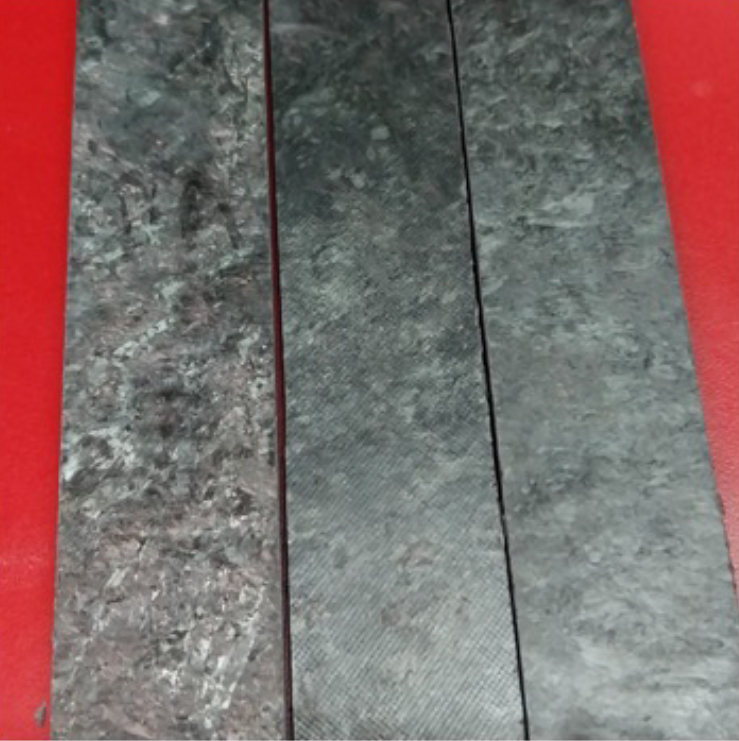
Cured carbon fibre recycling by chemical recycling
As an alternative to mechanical recycling, a solvolysis process using mild conditions is proposed to treat cured carbon composites with amine-hardened epoxy resins so that the fibres are recovered with all their properties and the organic matrix is materially valorised. The MC4 chemical recycling process is developed using initially referenced materials of known composition and validating the results with real waste streams. The recovered fibres show a resin-free surface and have mechanical properties comparable to those of virgin fibres.
The MC4 chemical recycling process uses acid solutions with high oxidative strength due to the high degree of crosslinking in the resins working below 100oC at atmospheric pressure and using industrially suitable reaction times. This allows the release of the reinforcing fibres and the degradation of the resin into a mixture of low and high-molecular-weight compounds.
The recycled carbon fibres (r-FC) obtained are a suitable material for manufacturing carbon prepregs that allow obtaining carbon composites with similar properties or those obtained from virgin carbon fibres. Additionally, the r-CF can be processed into nonwovens. However, a pre-opening of the fibres will be necessary to convert the fibre bundles into separate single fibres. The recovered organic fraction indicates the presence of high-value compounds useful for the manufacture of new polymeric compounds.

This work is licensed under Creative Commons Attribution-NonCommercial-NoDerivatives 4.0 International.