Professor Savvas Tassou, Brunel University London, discusses how waste thermal energy recovery and conversion to electrical energy can contribute to the decarbonisation of energy intensive industries
The potential of waste heat recovery and its conversion to useful energy is universally recognised. However, there are technical, economic and management challenges that need to be addressed for this potential to be realised. This article presents some of these challenges and research undertaken by the I-ThERM project to address both high and low-temperature waste heat recovery and conversion challenges. The work is funded by the H2020 programme of the European Union (EU) and UKRI’s (UK Research and Innovation) Programme.
Industry in the EU28 is responsible for approximately 25% of final energy use with almost three-quarters of this energy consumed by heating and cooling processes. Gas and electricity are the most dominant forms of energy in industry with gas being combusted in boilers and furnaces to provide direct heating to processes or indirect heating through the production of steam or hot water for space and process heating.
During the last fifteen years, the EU’s industrial energy consumption fell by 17% and the energy intensity (energy consumed per unit of production) by 25%. This is due to the implementation of low-cost energy efficiency measures with the potential for returns on investment of less than two years. Despite the progress achieved to-date, significantly more research effort is required for the development and implementation of new technologies and processes to meet the EU’s Greenhouse Gas Emission (GHG) reduction targets to 2050.

Combustion-based heat production processes in industry generate significant quantities of waste heat which can range from 30% to 50% of the energy input to the process. Depending on the process this heat is at different temperatures which can be classified as low, medium or high. This heat can be recovered and used directly within the process or industrial site, exported to neighbouring sites, upgraded to higher temperatures, or converted to other forms of energy such as high value electricity.
The potential of heat recovery in providing substantial energy savings in industry is now well recognised but to realise this potential there are a number of barriers to be overcome. These include: i) insufficient information on performance to provide confidence in the technology before it is implemented, ii) high initial and maintenance costs, iii) lack of infrastructure and space for the installation; iv) production constraints and risk of disruptions and v) lack of financial support and other governmental incentives.
Objectives of the H2020 funded I-ThERM project
To address some of the challenges and barriers to the application of heat recovery technologies, the I-ThERM (Industrial thermal energy recovery, conversion and management) project, aims to investigate, design, build and demonstrate innovative plug and play waste heat recovery and conversion solutions with high replicability and energy recovery potential in the temperature range 70ºC-1000ºC. The project involves 13 partners from across Europe, three large industry partners, seven small and medium companies (SMEs) and three Research and Technology Development (RTD) organisations, and is coordinated by Brunel University London. It is funded under the EC’s Horizon 2020 (H2020) programme EE-18-2015 ‘New technologies for utilization of heat recovery in large industrial systems, considering the whole energy cycle from heat production to transformation, delivery and end-use’.
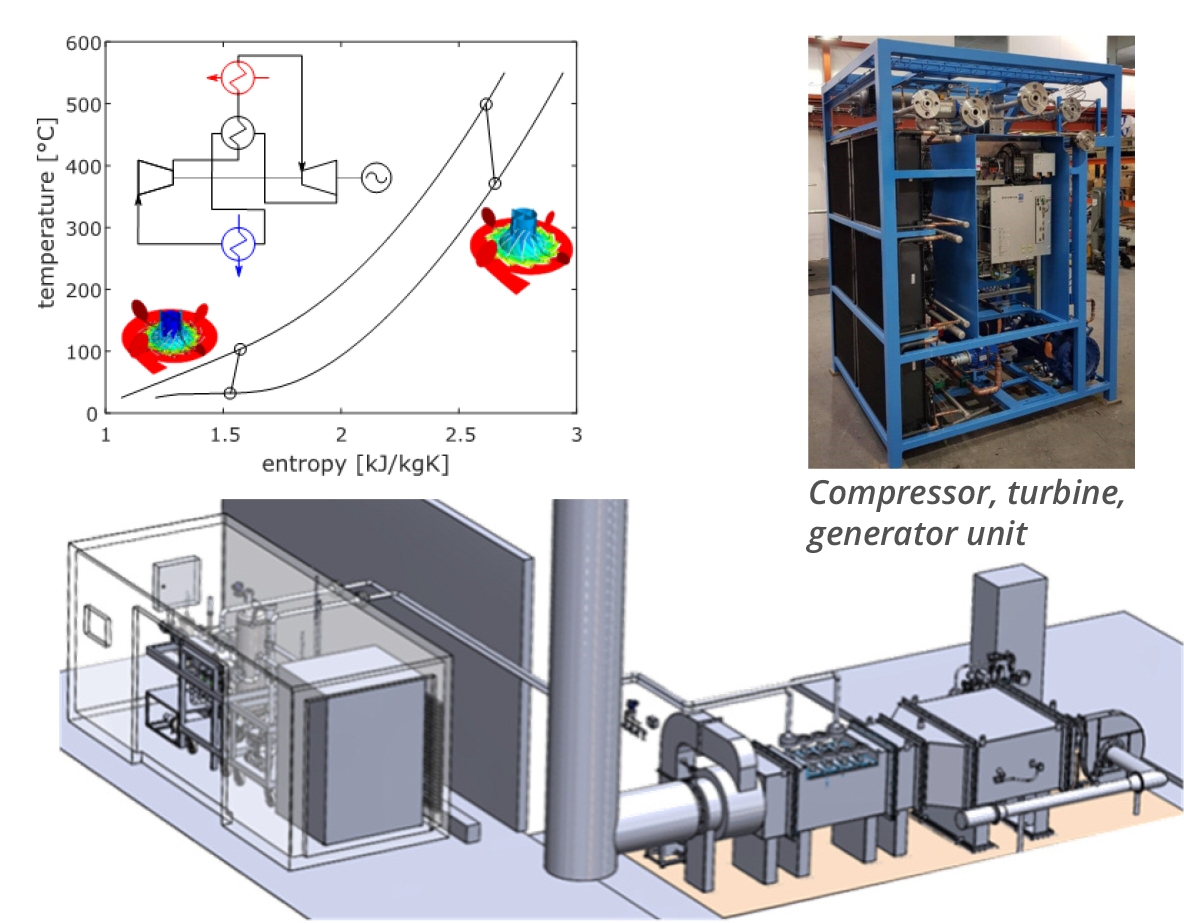
The main objectives of the I-ThERM project are:
- Development and demonstration of heat recovery equipment and systems in easily customisable plug and play forms based on the heat pipe technology. Two specific technologies will be developed. The Flat Heat Pipe System (FHPS) to recover heat from high-temperature radiant heat sources and the Heat Pipe Condensing Economiser (HPCE) to recover sensible and latent heat from corrosive exhausts.
- Development and demonstration of two innovative waste heat to electrical power conversion technologies, the Trilateral Flash Cycle (TFC) technology for low-temperature (70ºC-120ºC) applications and the supercritical Carbon Dioxide Technology sCO2 system for high-temperature (350ºC-800ºC) applications.
Progress to date
The project started in October 2015 and demonstration and evaluation of the technologies is expected to be completed by March 2020. The two heat recovery technologies have been designed and prototypes of the flat heat pipe technology have been constructed and successfully tested at the wire roll mill at Arcelor Mittal in Spain. The current focus with the heat pipe condensing economiser is on the development of coatings to protect the heat pipes against corrosion from the condensation of acidic components in the exhaust gases. Alongside this, attention is also placed on heat transfer enhancement and condensate drainage from the pipes.
The trilateral flash cycle heat to power conversion system
A significant proportion of the waste heat available from industrial processes is at low to medium temperatures. Many of these processes and industrial sites do not have the need for additional heat and so there is considerable interest to convert this heat to high-value electricity. Organic Rankine Cycles (ORCs) which are reasonably established as heat to power conversion devices have relatively low efficiencies at low-temperature applications. The TFC system being developed in the I-ThERM project aims to fill this gap. Figure 1 shows a schematic diagram of the cycle and a picture of the demonstration unit under development. The system will be installed and demonstrated at the Tata Steel manufacturing site at Port Talbot in the UK by Spirax Sarco UK.
The supercritical CO2 heat to power conversion system
Currently, there are no packaged plug and play systems available in the market for high-temperature waste heat to power conversion. The I-ThERM project aims to develop and demonstrate such a system for the first time in the EU using the Brayton cycle and supercritical CO2 as the working fluid. Figure 2 shows a schematic diagram of the basic cycle and the test and demonstration facility for the system. The sCO2 system has the potential for direct heat recovery, high-temperature and pressure operation, high efficiency and very compact size. The high temperatures and pressures also present challenges in heat exchanger design, material selection, and development of the compressor-turbine-generator unit. These challenges are being addressed in the project.
Concluding remarks
The technologies being developed in the I-ThERM project are designed to address both technical and economic challenges for both low and high-temperature waste heat recovery and conversion to electrical power. Evaluation of the technologies will be performed through installation and monitoring at industrial sites for demonstration purposes. This will be followed by further development and commercial exploitation.
Please note: This is a commercial profile
Professor Savvas Tassou
Director, Institute of Energy Futures
Brunel University London
Tel: +44 (0)189 526 6865
https://www.brunel.ac.uk/research/Institutes/Institute-of-Energy-Futures