Stuart Lyon, AkzoNobel Professor of Corrosion Control, explores how corrosion remains a significant cost to industrialised economies and the importance of corrosion protection
Back in the day, it was quite common for car vehicle bodies to suffer from rust perforation within a few years of purchase. Now manufacturers offer anti-perforation warranties for up to 12 years. It’s not that the steel has got any better or road de-icers are less salty; it’s that we have all gotten a bit wiser.
What is corrosion, and what are the costs?
Corrosion – the deterioration and loss of materials and their functional properties by environmental exposure – remains a significant cost to industrialised economies. Over the last 50 years, surveys in the UK, USA, China and elsewhere have consistently put the costs of corrosion between 2.5 and 4% of GDP. And while this figure is hard to grasp, applied as straight-line depreciation it means that, on average, everything around us loses all economic value and/or function in around 30-50 years – simply due to corrosion. Fundamentally corrosion is a consequence of the thermodynamic tendency for materials to revert from whence they came. Even rocks and stones weather away but only gold remains. So, although it can never be beaten, fortunately, corrosion can be controlled.
Let’s paint it: paint coatings for corrosion protection
The most practical and effective means of protection is to apply a coating, and the most widely used are paint coatings. However, these are not from the cans available in hardware stores for household decorations. Corrosion-protective organic coatings are engineered to optimise application (onto challenging surfaces) and lifetime performance. They comprise many ingredients including functional pigments that chemically inhibit the corrosion process, components that provide desired physical properties including hardness, wetting agents, rheology modifiers to enable correct surface flow from spray or brush application, etc. These components are held together by polymeric (generally cross-linked plastic) binders which are tuned to “cure” (i.e. harden) in just the right length of time. Such coatings can have exceptional performance, especially when applied under controlled conditions. For example, it’s not uncommon for engineered coatings on building claddings (i.e. siding and roofing) to have warranties in excess of 30 years.
Extending the lifetime of assets by application of corrosion protective coatings is thus a proven means of sustainably using materials and reducing the consumption of scarce resources. Coating performance has improved over many years of research, testing and experience, but the best available performance, from current technologies, is delivered by solvent-based coating systems containing materials that may be subject to future controlling legislation or may become unavailable in the market at an acceptable cost. Challenges therefore revolve around making the coating itself more sustainable, for example by lowering embedded carbon which effectively means moving from current solvent-borne formulations to future water-borne formulations.
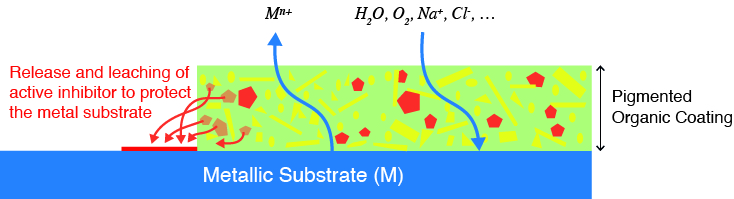
Water-borne (or emulsion) paints are, of course, available in the above-mentioned cans for beautification of internal spaces. Although water-borne formulations have many strengths and advantages, their performance as corrosion preventative coatings does not currently come close to solvent systems. One day you might be able to paint ships, aeroplanes, cars and bridges with emulsion paint and expect it to perform in the same way as a solvent-based paint, but not just yet.
Watching paint dry: long-term corrosion testing and evaluation
The formulation of complex products containing many ingredients has occasionally been called more art than science and if something works, it is very difficult to change. Traditionally, novel formulations are based on years of experience and extensive laboratory and field / service testing. This process generally works very well and is not going to change any time soon. However, reasonable expectations of long-term performance require long-term corrosion testing and evaluation, so this process is not quick or agile. Starting from the 1960s It took over 20 years to identify an effective substitute for lead-based corrosion protective paints and after a further 40 years we are still trying to eliminate the last use of strontium chromate for corrosion protection on aircraft.
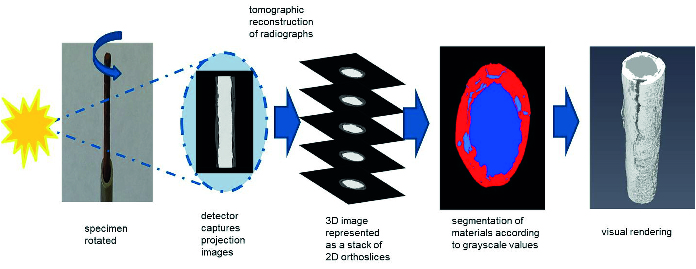
Figure 2: X-ray tomography: paint coating (red), steel wire (blue) and paint defects (light blue)
With today’s increasing emphasis on materials sustainability which is driving the move to high-performance water-based coating systems it is no longer desirable, practical, or possible to use the tried and tested methods. In order to shorten the development pathway a much greater fundamental and mechanistic understanding of “how paints work” is needed by the application of high-resolution analytical tools to probe the structure and chemistry of coatings and the interfaces between their constituent parts. So, contrary to the old adage, watching paint dry is both the opposite of boring and the only way that the performance of novel, sustainable coatings formulations can eventually match those of traditional systems.
The Corrosion@Manchester research group in the Department of Materials comprises a team of 8 academic staff, and over 60 researchers and is supported by over 30 national and multinational businesses. It is Europe’s largest university-based activity concerned with corrosion protection and materials performance and has an international reputation for research excellence and innovation.

This work is licensed under Creative Commons Attribution-NonCommercial-NoDerivatives 4.0 International.