Dr Carlos Ziebert, Leader of the Group Batteries – Calorimetry and Safety, KIT, explains how online venting gas analysis of batteries can be performed using a combination of battery calorimetry and online mass spectrometry
The main objective of the AnaLiBa project (Analytics of LithiumIon- Batteries) is the joint method development of a standardised sample handling process for the gas analysis of large cells by combining an accelerating rate calorimeter (ARC) and online mass spectrometry (MS).
It is a part of the competence cluster Analytics/Quality Assurance (AQua) funded by the German Federal Ministry of Education and Research (BMBF). The Fraunhofer Institute for Chemical Technology coordinates the project.
The other partners are the Centre for Solar Energy and Hydrogen Research BadenWürttemberg (ZSW) in Ulm and the Institute for Applied Materials – Applied Materials Physics (IAM-AWP) of the KIT. The AnaLiBa developments encompass at first the direct insertion of a capillary into the cell, which is attached to a pressure sensor; at second, a method in which a pressure- tight canister is connected via a capillary to a gas collection device; and at third, a direct coupling of the canister and an online mass spectrometer.
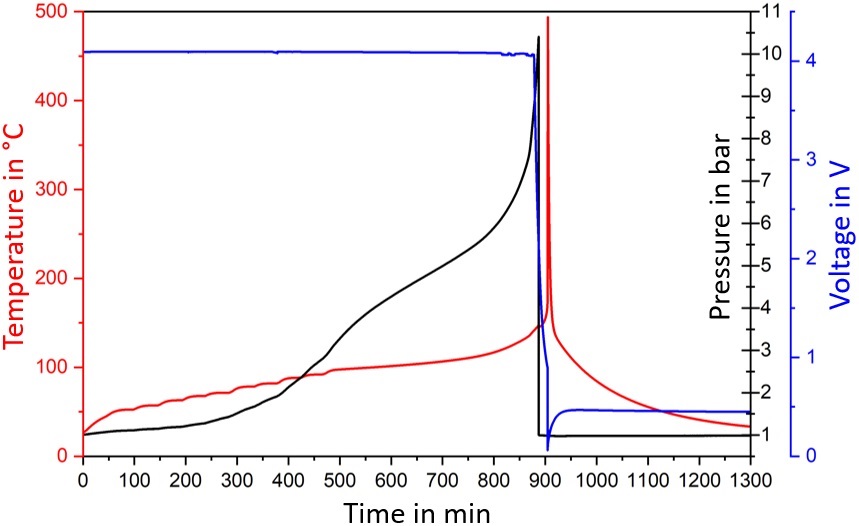
Online pressure measurement
For the first method, Figure 1 shows the temperature (red curve), the cell voltage (blue curve) and the internal pressure (black curve) vs time of a 21700 cylindrical cell with inserted capillary during a Heat-Wait-Seek test in a battery calorimeter. (1)
It can be clearly seen that the safety vent of the cell vents (opens), when an internal pressure of 10.5 bar is reached due to the gases formed during exothermic reactions. Shortly after this venting, the cell goes into thermal runaway and reaches up to 500 °C. The second method was presented in our previous article. (2)
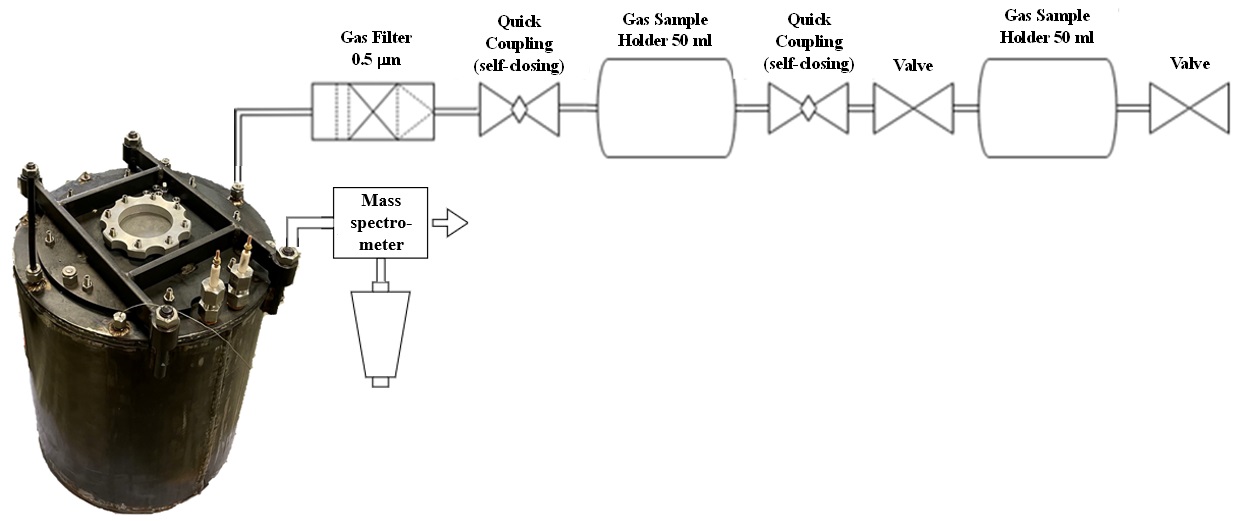
Online mass spectrometry
Figure 3 shows an example of an overcharge test in which the direct coupling of an ARC to an online mass spectrometer provided by the project partners from ICT was realized. A 4 Ah Lithium polymer pouch cell was put into the pressuretight cylinder shown in Figure 2 and overcharged with a 1C rate (4 A), until thermal runaway occurs, indicated by the maximum temperature of 400 °C.
It can be clearly seen that hydrogen, carbon monoxide, carbon dioxide, methane and ethane have been formed. Whereas the first three gases are mainly produced by the thermal decomposition of EMC or DMC, the methane and ethane can be attributed to decomposition reactions of the solid electrolyte interface (SEI), which is a protective layer on the graphite anode that is built up during the first charging and discharging processes, the so-called formation procedure. The different presented methods elucidate the relevant decomposition paths and help develop suitable safety measures to prevent thermal runaway or prolong the thermal propagation in a battery module.
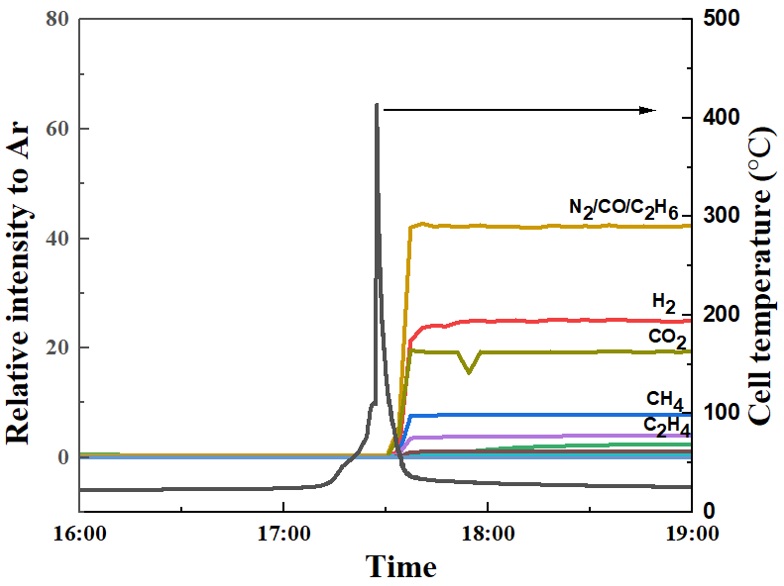
References
- Increasing electric car battery safety using calorimeters, Open Acess Government 31, July 2021, pp. 382-383.
- Battery venting gas analysis using battery calorimeters & gas chromatography, Open Acess Government 33, January 2022, pp. 384-385.

This work is licensed under Creative Commons Attribution-NonCommercial-NoDerivatives 4.0 International.