Due to the inevitable variability of the end-of-life input material, the resulting recycled fibre and nonwoven or woven material will have a higher degree of variability than virgin material. To make sure such recycled fabric is usable for high-quality applications, additional methods for quality control are required
Existing methods for quality control, such as the Profactor FScan sensor, are used to detect a range of different types of deviations during the manufacturing of carbon fibre fabric. Such sensors can be integrated into weaving machines to cover the whole width of the material (e.g. up to 2.5m) and identify defects in real time.
Identifying defects
The defects to be found include deviations in the weaving pattern, gaps, missing sewing yarns, deviations in fibre orientation, foreign objects, and fuzzballs. Also, the inspection methods have been developed to work with any kind of material, including dry material, prepreg and carbon fibre with binder, and they are also independent of the particular weaving pattern, including uni-directional fabric or woven material.
For recycled material, however, existing quality control methods have to be extended to account for the different appearance of the materials and quality criteria are still to be developed. Nevertheless, the different characteristics of the chopped fibre already indicate which properties will be relevant. Due to the manufacturing process, the fibres will be randomly oriented but will not be isotropic.
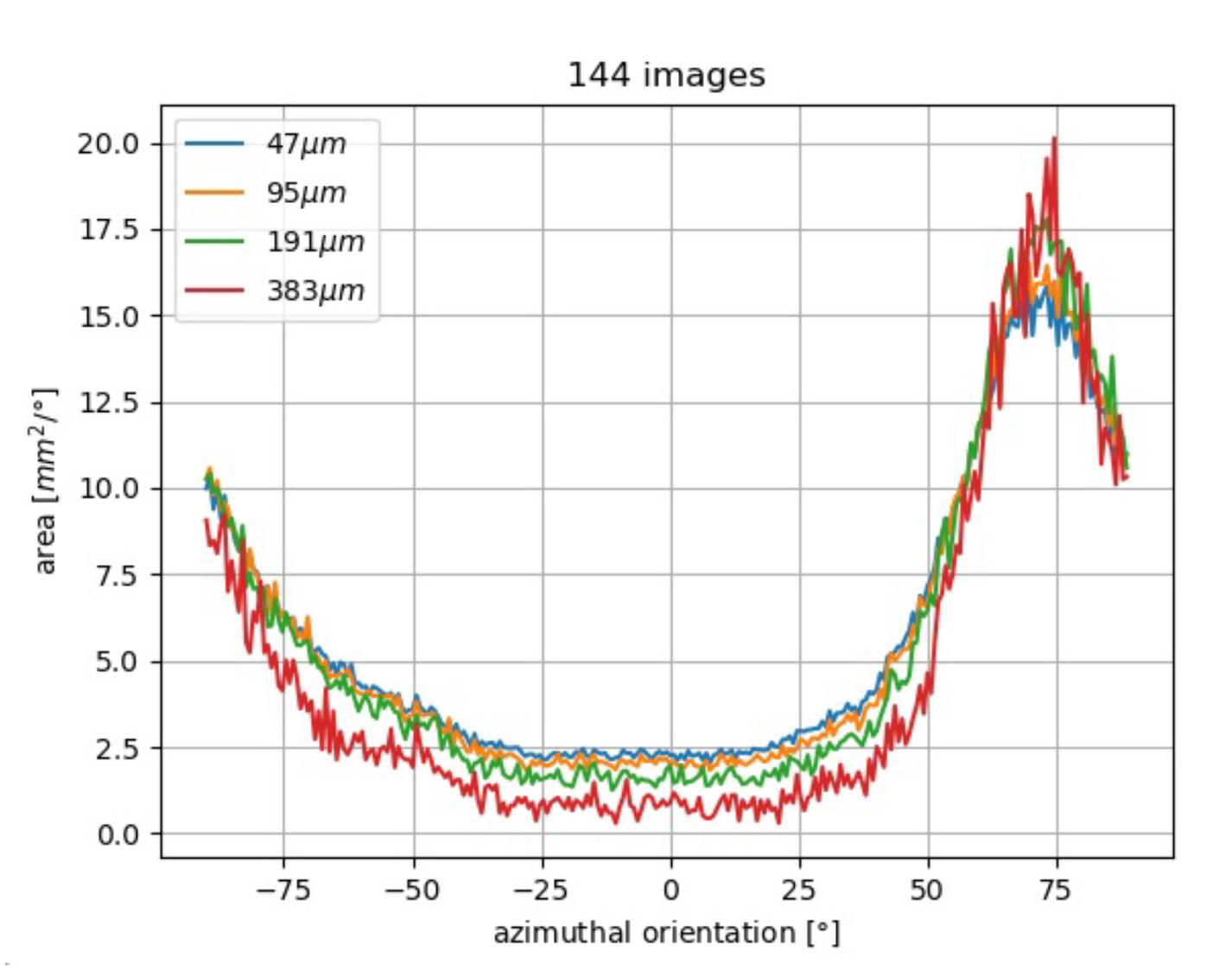
The histogram shows a peak at about 75°. The spreading of the orientations indicates the mechanical properties of the material
Obtaining a complete histogram of fibre orientations
To optimise the material’s performance, it is beneficial to create some kind of ‘main direction’ of the fibres. During quality control, it is thus important to determine a full histogram of fibre orientations, estimating the amount of fibres that are oriented in a particular direction. The machine vision technology used in the FScan sensor allows the calculation of such fibre orientation histograms independent of the particular design of the material.
This kind of quality control allows the different materials to be graded according to their performance and thus be used in suitable applications. This will minimise the need for downcycling and allow expensive carbon fibre to remain in a circular process for a more extended period.

This work is licensed under Creative Commons Attribution-NonCommercial-NoDerivatives 4.0 International.