When the PHERA Project started, it was with an ambitious goal to prove that insect pheromones can be produced using a biological rather than a chemical process. A seeming subtlety, yet with the potential to propel agriculture in a much more sustainable direction involving less pesticides. Now, nearing its end, the EU-funded PHERA Project reveals just how far it has come
When modern insecticides were introduced around World War II, it was accompanied by optimism. Insecticides quickly helped to boost agricultural output for a growing global population. In time, however, concerns arose about their environmental and human impacts. Insecticides also became less effective as insects developed resistance to them. Instead, integrated pest management (IPM) became more prevalent.
IPM entails using a range of biological, physical and chemical methods to monitor, prevent and control pests. The idea is to keep pests below economically damaging levels without solely relying on pesticides. With insect pheromones offering farmers another and more environmentally friendly mode of action than insecticides, they are perfectly suited for IPM.
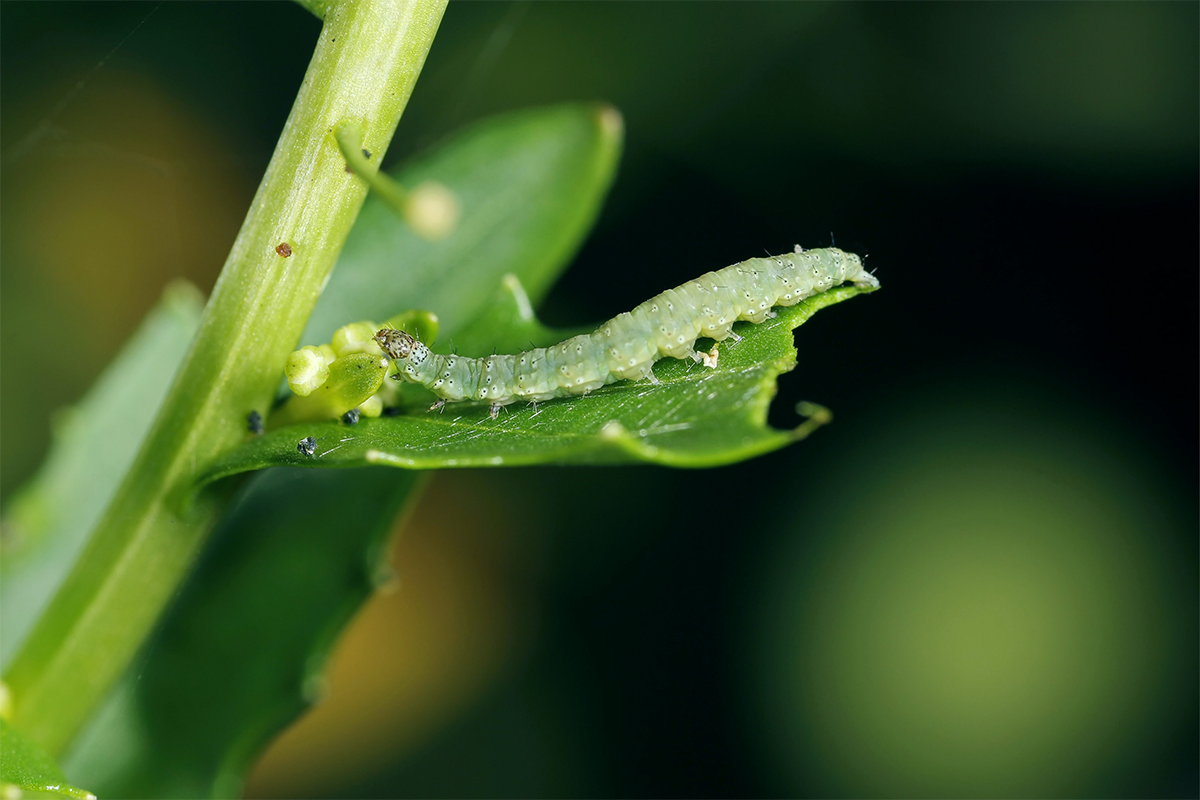
PHERA scales up a new manufacturing platform for pheromones
What the PHERA Project has accomplished is to facilitate the optimisation of a biological manufacturing platform for pheromones, building on the innovative science of one of its partner companies, BioPhero, now owned by FMC Corporation. When the PHERA Project started in March 2020, BioPhero had demonstrated that it was possible to produce one specific pheromone using yeast fermentation, and only in small quantities, a far cry from producing the tonnes of pheromones needed for practical application in fields. This is all history, explains Jesper Dohrup, Operations Lead, Pheromones, Global Plant Health, FMC, who has overseen the expansion of production at BioPhero.
“Under the auspices of the PHERA Project, we have scaled up our technology platform to full industrial production, developing our own industrial processes from scratch. Using a combination of biological yeast fermentation and subsequent chemical processing, we can now produce three pheromones at a competitive cost,” he says.
Yeast fermentation lowers the cost of insect pheromones
Insect pheromones have traditionally been manufactured via chemical synthesis; an expensive process due to the complexity of pheromones. The high cost has limited their use. In contrast, yeast fermentation makes it possible to mass-produce pheromones at a cost that can compete with insecticides. This expands their use from winegrowing and other high-value fruits and vegetables to the large row crop market.
“Since pheromone products offer farmers a sustainable way of protecting crops, our guiding principle has also been to make our manufacturing processes as sustainable as possible, using renewable raw materials and incorporating safety and environmental considerations right from the start,” Jesper Dohrup explains.
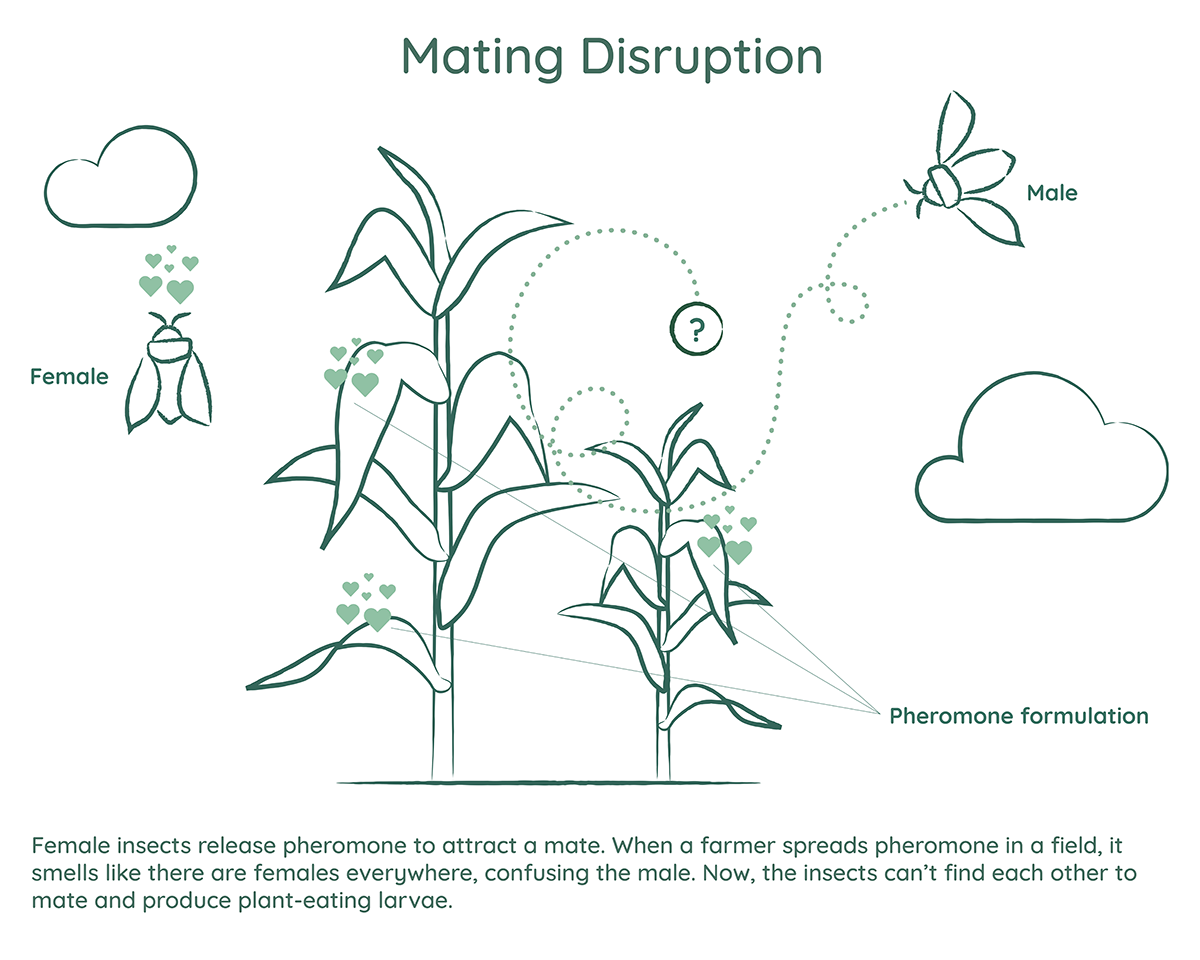
Minimising waste and maximising recycling
Guided by the classification of industrial sites outlined by the EU Seveso Directive, BioPhero designed its production to comply with the lowest category of risk. For example, this means minimising waste and including a high degree of recycling of auxiliary substances.
The pheromones are now moving into the fields. BioPhero’s partners have developed long-acting pheromone formulations that are convenient to use. For instance, NovAgrica has developed a formulation for drone application as well as hydro-degradable dispensers that do not have to be replaced. Russell IPM has developed biodegradable dispensers, which in field trials in Bangladesh and India increased the yield by 25% whilst reducing insecticide consumption.
The PHERA Project
The PHERA project aims to further sustainable agriculture by establishing insect pheromones as a viable alternative to insecticides in row crops. The project is scaling up a new, cost-effective method for mass-production of pheromones and is developing application systems for their use in pest control in row crops.
The project partners include BioPhero (fermentation); SEDQ, ISCA, Russell IPM and NovAgrica (formulation and application); Bioprocess Pilot Facility (pilot plant); and Fraunhofer (life cycle analyses).
This project has received funding from the Bio-based Industries Joint Undertaking (JU) under the European Union’s Horizon 2020 research and innovation programme under grant agreement No. 886662. The JU receives support from the European Union’s Horizon 2020 research and innovation programme and the Bio-based Industries Consortium.

This work is licensed under Creative Commons Attribution-NonCommercial-NoDerivatives 4.0 International.