The effect of carbonation induced corrosion on reinforced concrete must be addressed both for safety and environmental reasons, say researchers from ETH Zurich
Carbonation means the progressive neutralisation of the alkaline constituents of concrete by carbon dioxide in the air, forming mainly calcium carbonate. In this neutralised environment, reinforcing steel is no more protected by the alkaline pore solution of fresh concrete. When the carbonated surface zone reaches the depth of reinforcing steel, significant corrosion may be initiated.
Indeed, corrosion of steel in carbonated concrete was a major concern of research and practice in the years from 1950 to 1980. The research findings lead to the requirement of dense concrete (lower w/c ratio), the control of concrete properties and to a marked increase in the cover depth (from 20 mm to 35 mm) in the codes of practice. The European standard on concrete EN 206-1 published in the year 2000 classified the risk of carbonation-induced corrosion depending on the severity of the environment (XC1 to XC4). With the minimum requirements given in the recommendations (maximum w/c ratio, minimum cement content, minimum cover depth) the codes of practice since then give guidance for reinforced concrete made with Portland cement (CEM I) on how to avoid carbonation induced corrosion for structures with expected service life of 50 or 100 years.
CO2 emissions
The role of carbonation as a factor that contributes to the degradation of reinforced concrete is becoming increasingly important again (Figure 1) for two reasons. First, many old reinforced concrete structures that were built before modern standards were applied are ageing and have to be maintained. Secondly, the need to reduce CO2 emissions and to obtain materials having a reduced environmental footprint, is leading to a reduction of the clinker content in the cements. Clinker (CEM I) is substituted with supplementary cementitious materials (SCM) such as limestone, fly-ash, geopolymers etc. In the future blended cements with increasingly lower clinker content and a huge variety of supplementary cementitious materials (SCM) will be used. The introduction of non-Portlandite binders has strongly reduced the pH buffer capacity as a result of the reduction (or elimination) of the calcium hydroxide reserve considered one of the main reasons for the corrosion inhibiting nature of Portland cement systems. The carbonation rate of such modern blended cements is a factor of 2-4 higher than for Portland cement (figure 2), thus the recommendations based on the experience with Portland cement do no more guarantee the required service life.
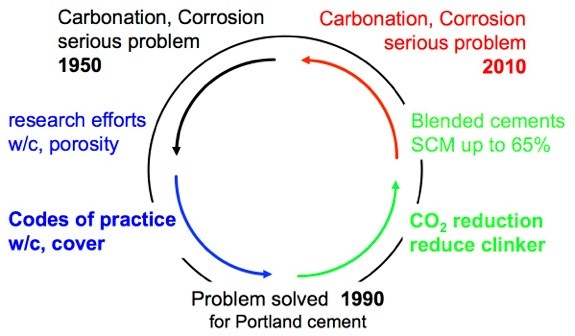
[1] A. Leemann, P. Nygard, J. Kaufmann, R. Loser, Cement and Concrete Composites 62 (2015) 33 – 43
[2] M. Stefanoni, U. Angst, B. Elsener, Innovative sample design for corrosion rate measurement in carbonated concrete, presented at 11th annual International Concrete Sustainability Conference (2016 ICSC) May 15 – 18, 2016, Washington DC (USA)
Prof Dr Bernhard Elsener
Head, Durability Research Group
elsener@ethz.ch
http://www.ifb.ethz.ch/corrosion
Matteo Stefanoni
Prof Dr Ueli Angst
Institute for Building Materials, ETH Zurich
Please note: this is a commercial profile