Laban Coblentz, Head of Communication at ITER takes us on a journey of discovery when it comes to fusion as a clean, safe, virtually unlimited source of energy for thousands of future generations
Cradled in the rolling hills of Haute-Provence in southern France, a slumbering giant is emerging from the earth. Global awareness is also rising: the ITER Tokamak, a collaboration of 35 countries to build the first industrial-scale fusion reactor – literally “a star on earth” – is among the most ambitious scientific endeavours of our time, with high stakes for our future.
While hundreds of tokamaks have been built over the past six decades, none are like this. Still, observers tend to limit their observations of ITER’s uniqueness to superlatives. The 150 million ºC operating temperature of the plasma. The frigid chill of the superconducting magnets, operating at near absolute zero (-269 ºC). The weight of the Tokamak Complex – 400,000 tonnes, heavier than the Empire State Building – resting on 493 carefully positioned seismic pads. The strength of the Central Solenoid structure at the machine’s heart, able to withstand twice the thrust of a space shuttle launch. Or the heat flux ITER’s toughest surfaces must withstand 20 megawatts per square metre, twice the torrid load a space shuttle endures on re-entering the Earth’s atmosphere, but for a sustained period.
These comparisons can be mindboggling. But they do not fully portray ITER’s “firsts,” nor do they hint at ITER’s ongoing, real-time return on investment for its partners. Within this first-of-a-kind machine is a miniuniverse of first-of-a-kind components, systems, and technologies.
Consider the ITER magnet system, designed to forge an invisible magnetic chamber inside the metal tokamak, confining the ultra-hot plasma away from the physical walls. To build this first-of-a-kind structure at ITER’s scale required, among other materials, 100,000 kilometres of niobium-tin strand, nearly 500 tonnes. At the outset, worldwide production capacity of niobiumtin stood at 15 tonnes per year. Nine suppliers in six of the seven ITER Members ramped up global output to nearly 150 tonnes per year – each working to precisely the same materials specifications, testing protocols, and quality assurance standards. A global industry was born. For any superconductor application, such as medical scanning equipment, a call for tender could now be placed with equal confidence in Carteret, New Jersey, Xi’an, China, or the Jastec facilities in Japan.
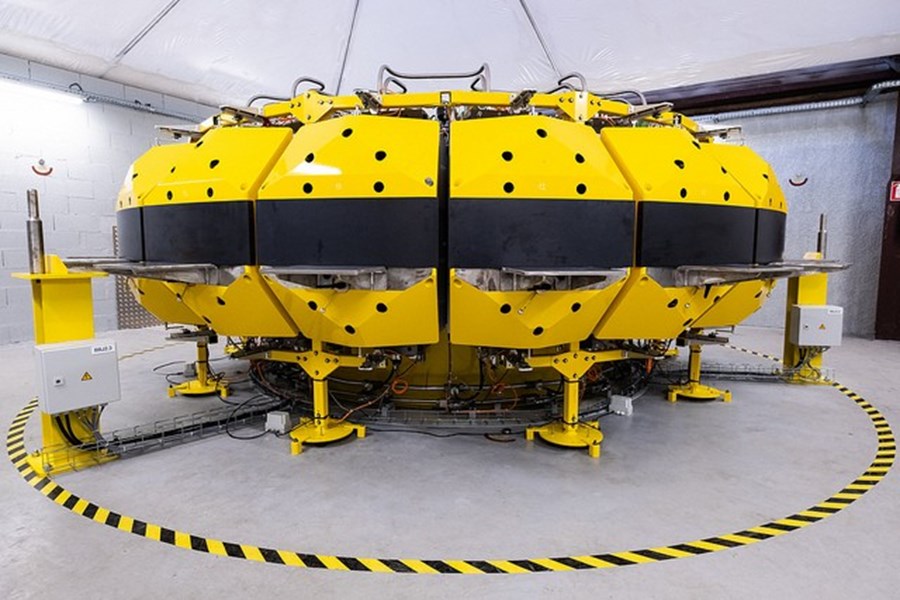
of ITER’s “pre-compression rings” (Image: © Fusion for Energy)
Consider the first-of-a-kind tools demanded by ITER’s assembly process. Taekyung Heavy Industries of Korea has manufactured the twin titans in this ITER toolbox: two 22-metre-tall Sub-Sector Assembly Tools, each capable of delicately folding together a 440-tonne vacuum vessel sector, two 310-tonne toroidal field magnets, and segments of the thermal shield into a composite whole, with precision measured in millimetres. To verify the performance of ITER’s magnet-protecting “pre-compression rings” – more than a billion glass fibres held together with epoxy resin – a futuristic testing device developed by Douce Hydro of France (pictured above) will exert a force of 36,000 tonnes with a positional accuracy of 0.1 millimetre.
Each such tool – and there are dozens more – demands innovation. And there is more. Across every aspect of the project, in laboratories and fabrication centres on three continents, fit-for-purpose R&D is being used to develop specialised steel alloys, gyrotrons, pellet injectors, power electronics, cryogenic pumps, tritium breeding systems, and hundreds of other first-of-a-kind innovations.
When CEOs talk about the benefit of participating in this project, they rarely focus on a contract’s monetary value. They speak of being stretched, of the creativity and innovation ITER demands, of the newly developed industrial capacities that result, of new spin-off technologies with implications and markets well beyond plasma physics or tokamak engineering – and of the increased competitiveness they acquire by being part of this unprecedented project.
The multinational nature of the ITER project is in itself driving first-of-a-kind solutions to logistics, shipping and storage, schedule management, 4D software and data management, multi-sector cooperation, and other challenges of international project management. Given the array of complex cross-border threats facing modern society, from climate change to pandemics, several wise observers have commented that the lessons learned in this area may prove to be among our most enduring and meaningful contributions: learning how to work together, in the most tangible terms, to solve a global problem.
Ultimately, ITER will enable scientists to study a controlled “burning” or self-heating plasma, the gateway to offering fusion as a clean, safe, virtually unlimited source of energy for thousands of future generations. But until that time, even now, the returns on investment are rolling in.
Laban Coblentz
Head of Communication
ITER
Tel: +33 4 42 17 66 17
It’s obvious that “unlimited energy” is going INTO this project.
No energy will ever come out.