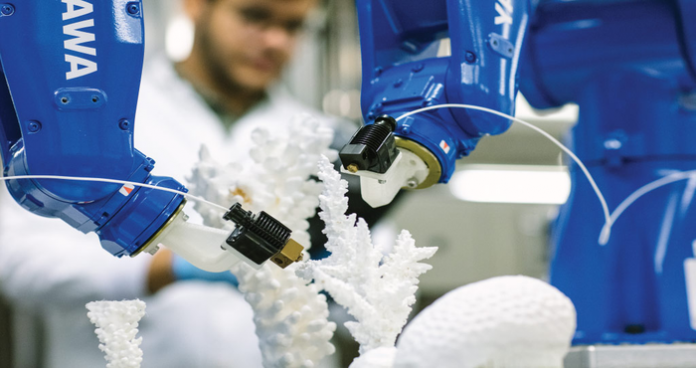
Global warming continues to bleach the coral reef, destroying marine ecosystems – but scientists believe the future of coral restoration lies in 3D printing
Coral reefs are one of the most biodiverse ecosystems in the world, supporting over 25% of all marine life. They are also rapidly disappearing and degrading, as global warming appears to increase.
At this moment, scientists are working on coral restoration. This is a wide umbrella term, describing various techniques to fix and conserve the coral reef, globally.
One of the best existing techniques is the process of microfragmentation.
Firstly, what is microfragmentation?
The discovery of microfragmentation came when Dr David Vaughan found a small coral specimen that had broken off from a larger one in the lab. The breakthrough allows coral to grow up to 40 times faster than previously before in the wild. Coral usually takes 25-75 years to achieve sexual maturity. The microfragmenting process speeds up the maturation process, allowing it to happen in just three years.
Now, scientists are looking to refine his technique – to encourage as much coral restoration as possible, in an even shorter window of time.
In new research by King Abdullah University of Science and Technology (KAUST), a team is using 3D printing to speed-up microfragmentation.
“Coral microfragments grow more quickly on our printed or molded calcium carbonate surfaces that we create for them to grow on because they don’t need to build a limestone structure underneath,” said Hamed Albalawi, one of the lead authors of the new study.
The idea is to give the corals a head start.
So, how does the 3D printing technique work?
The technique, known as 3D CoraPrint, uses an ecofriendly calcium carbonate photo-initiated (CCP) ink – also created by this team.
3D CoraPrint involves attaching coral microfragments to the printed skeleton to start the process. It also incorporates two different printing methods, both of which start with a scanned model of a coral skeleton.
In the first method, the model is printed, and the print is then used to cast a silicon mold. The final structure is produced by filling the mold with CCP ink.
In the second method, the support structure is printed directly using the CCP ink.
“With 3D printing and molds, we can get both flexibility and mimicry of what’s already going on in nature,” said Zainab Khan, the other lead author.
“The structure and process can be as close as possible to nature. Our goal is to facilitate that.”