The development of more sustainable technologies for energy-intensive industry is imperative to meet the ambitious targets that UK and Europe have recently announced by 2050
The net-zero innovation platform recently issued by UK government mostly rely on renewable technologies that will enable the electrification of several sectors including power generation as well as other very energy and carbon-intensive industries such as steel manufacturing, cement, chemicals.
Some of these processes are hard to decarbonise given the variety of streams and complexity of the process, as well as the difficulties to retrofit or combine with electrification or green sources such as biomass or hydrogen from electrolysers.
To help the transition towards net zero and at the same time reduce the operational costs of these processes, waste valorisation should be pursued generating additional revenues and reducing the overall carbon emissions into the atmosphere.
At the University of Manchester, we are committed to clean and sustainable chemical processes, and we are developing next generation cutting edge technologies to teach future engineers and at the same time we work closely with industries to move innovation from laboratory to industrial settings.
Several research projects are currently ongoing specifically looking at new and more sustainable technologies by waste valorisation to produce hydrogen and other relevant chemicals for energy and transport applications.
Our laboratories are located in the James Chadwick Building, a three-stores building used for undergraduate teaching laboratories, fundamental research and pilot scale processes, fully integrated with advanced control systems.
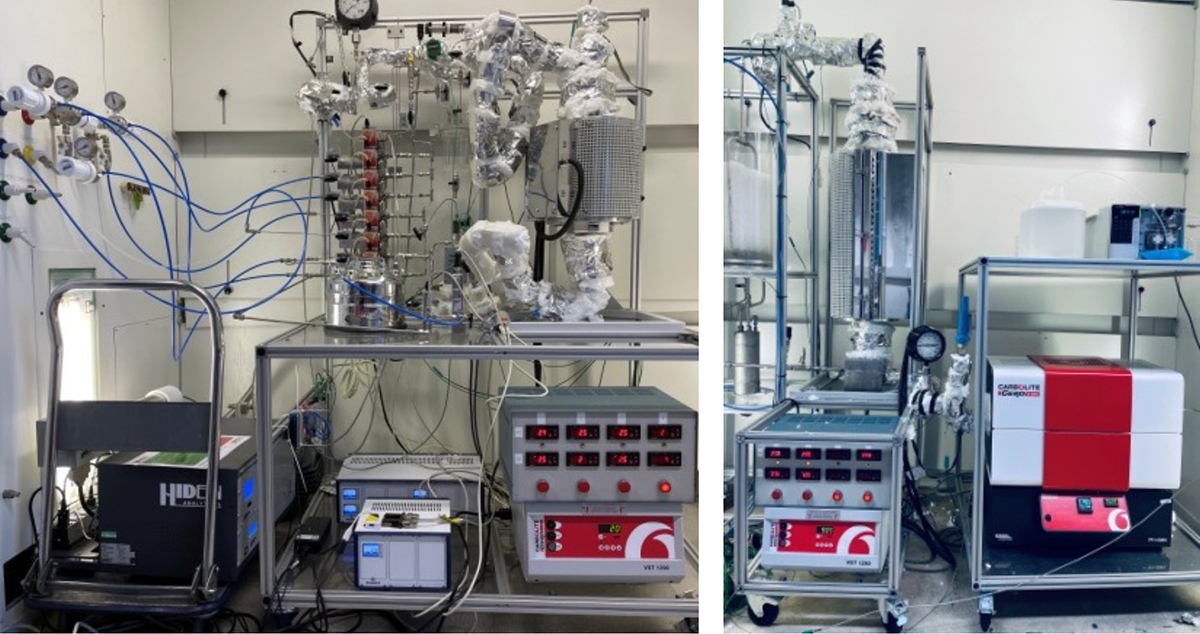
Waste glycerol to added value products (H2020 GLAMOUR project)
Glycerol is an abundant by-product of biodiesel plants as well as other bio based feedstocks. The University of Manchester is leading the H2020 GLAMOUR (Glycerol to Aviation and Marine products with sustainable Recycling). The 4 years project has
received a €5 million grant from the European Union’s Horizon 2020 programme, and officially started on May 2020.
The aim of the project is to convert waste glycerol from 1st and 2nd generation biodiesel plants into sustainable aviation and marine fuels. The H2020 GLAMOUR project is a broad collaboration covering the complete value chain from feedstock supplier to end-users.
Coordinated by the University of Manchester, the consortium includes two universities, three research centres and five industries (including 2 SMEs) with participants from six EU countries (Figure 2).
This project is looking at three integrated technologies and by the end of the project, the GLAMOUR technology will reach a TRL5 demonstration innovating in material science, process engineering, sustainability and socio-economic studies.
Main technologies which are currently under study are:
Waste glycerol refining
by combining physiochemical processes (Figure 3) and advanced analytical data processing methods led by Argent Energy in collaboration with the University of Manchester. Current advances within the state-of-the-art includes electric driven process testing to further reduce the impurities of the feedstock.
Glycerol gasification
the purified glycerol is converted into syngas via chemical looping reforming in packed bed reactors. This process – developed in the past 6 years by the University of Manchester and TU Eindhoven – relies on the use of an oxygen carrier and
catalyst which produce syngas while separating CO2 at high purity that is suitable for storage or utilisation.
Fuel synthesis via Fischer-Tropsch reactor
the conversion of syngas into sustainable aviation and maritime fuels occurs via 3D-printed structured reactor to achieve high yield, and efficient thermal management.
The pilot plant is under construction at TU Eindhoven and the testing campaign will start in the next year to produce overall 0.5 kg per hour of Syncrude for 1,000 hours. The conceptual design at industrial scale simulation is confirming the expected key performance indicators also in terms of life cycle assessment. Finally, the project has linked with >10 other European and national initiatives of next generation biofuels sharing joint communication and dissemination activities.

Hydrogen production from energy-intensive industry
Applications of a new intensified process using gas-solid reactions are
currently under development to produce hydrogen from different sources. After successfully demonstrating the use of blue and renewable-based hydrogen production with chemical looping reforming, we are preparing the feasibility study for the Department of Business, Energy and Industrial Strategy (UK) in collaboration with Johnson Matthey, TotalEnergies and Element Energy, to build the first modular and flexible hydrogen demonstration plant in Manchester within the next 4 years based on dynamically operated gas-solid reactors (BEISRECYCLE).
In terms of waste valorisation, a similar process is being studied using blast furnace gases from integrated steel mill. In Manchester, we are looking at new configurations that will integrate renewables energy (EPSRC BREINSTORM). However, a TRL7 demonstration of the 1st generation calcium0chemical looping process will be reached in 2024 under the H2020 C4U project (coordinated by UCL) through an international collaboration between CSIC, Arcelor Mittal, TNO, Carmeuse, Johnson Matthey and Manchester.
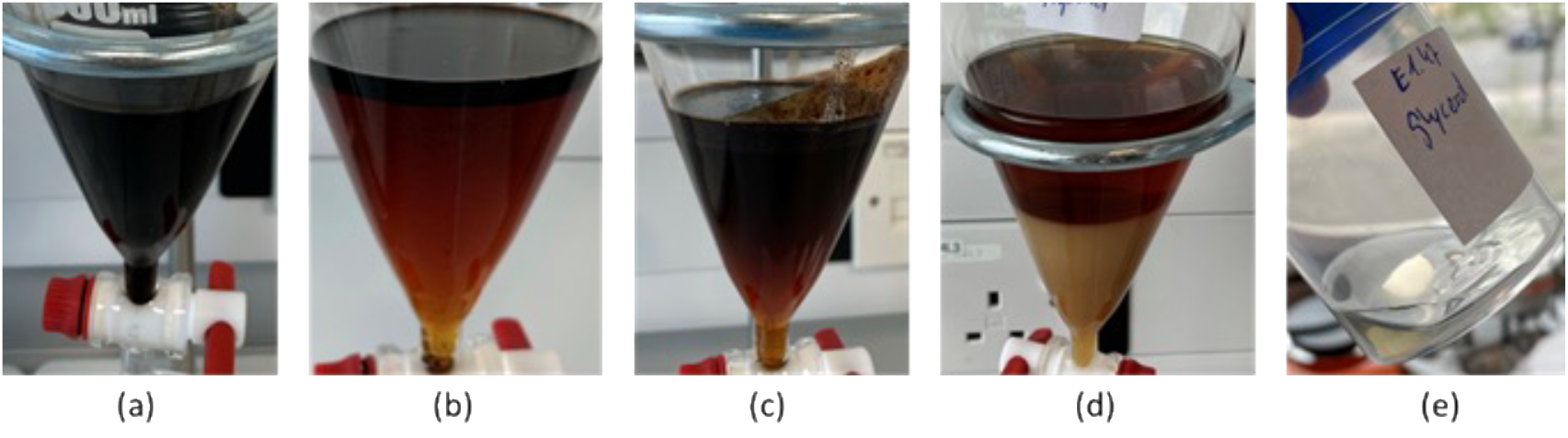
Acknowledgements
Vincenzo Spallina would like to acknowledge the EU Horizon 2020 research and innovation programme under grant agreement no. 884418 (https://c4u-project.eu/) and no. 884197 (https://www.glamour-project.eu/). The work reflects only the author’ view and the EU is not liable for any use that may be made of the information contained therein. The author would like to acknowledge also the Engineering and Physical Sciences Research Council (EPSRC) as part of the UKRI program (BREINSTORM – EP/S030654/1) and the Department of BEIS in the framework of the Low Carbon Hydrogen Supply 2: Stream 1 Phase 1 Competition – GOV.UK (www.gov.uk) (TRN 5044/04/2021) (RECYCLE: Rethinking low Carbon hydrogen production by Chemical Looping reforming, HYS2137) for providing funding and support to development of this study.
Please note: This is a commercial profile
© 2019. This work is licensed under CC-BY-NC-ND.