The University of Iceland charts the opportunities & challenges concerning the utilisation of geothermal energy, understanding high-temperature corrosion
The global chase for renewable and green energy has led to an increased requirement for geothermal power generation. In this regard, one of the key elements for higher well output and increased efficiency of geothermal turbines and production equipment is the reduction in mechanical energy loss and increased lifetime of materials. Materials used in geothermal systems which are in direct contact with the geothermal fluid can be subjected to corrosion, which can result in high costs associated with materials, labour, and production efficiency of the system.
The corrosion aggressiveness of geothermal fluids depends on the physical character and chemical composition of the fluid, as well as the exploitation parameters such as temperature, pressure and flow rate. The main corrosive agents in the geothermal fluid are the dissolved gasses such as H2S and CO2. Components used in construction of geothermal wells and production of geothermal power from high- temperature geothermal fields can experience different corrosion attacks as well as wear and erosion.
Energy efficiency & lifetime increased with more durable materials
To address these issues, we in the Materials Engineering and Corrosion Center at University of Iceland have participated in several research pro- jects with a focus on the development of coating materials as protection against such damages. These include the Horizon 2020 funded projects: Geo-Coat, GeoDrill and GeoHex.
At the Materials Engineering and Corrosion (MEC) Center, University of Iceland, the research focuses on material testing and corrosion research for the development and progress of novel materials for various demanding applications, particularly in the high temperature and corrosive environment for the utilisation of geothermal energy.
Deeper and hotter
Around the world, there has been an increased interest in exploring the deep roots of geothermal systems by drilling deeper geothermal wells with higher enthalpy fluids for potential utilisation. It involves subsequently higher temperatures (>300°C) and pressure (>100 bar) and a more corrosive environment than in typical high- temperature geothermal wells. Several material challenges are encountered in the design, construction and production of deep superhot geothermal wells. These include stresses and strain exceeding the yield strength and plastic strain limits due to the thermal cycling of carbon steel (CS) casing materials. Additionally, due to high temperatures and corrosiveness of the geothermal fluid, increased corrosion and erosion-corrosion can be expected. The CS casing materials also lose their strength at elevated temperatures; therefore, lower loads are needed for failure.
The CS casings commonly used in these projects are not corrosion resistant and are susceptible to various corrosion forms such as hydrogen embrittlement, sulphide stress corrosion cracking and microcracking due a high-temperature hydrogen attack. Thus, materials that have higher corrosion resistance and better resistance against thermal cycling effects are needed to achieve the structural integrity of superhot wells.
In an effort to fill the knowledge gap that exists in this field, Prof Karlsdottir’s research group and collaborators, Gerosion Ltd., have been undertaking research on the corrosion behaviour and high-temperature stability of casing materials in the superhot and supercritical geothermal environment. Recently, their project called “Material Research and Modeling for High Temperature and Superhot Deep Geothermal Wells” received funding from the Icelandic Centre for Research.
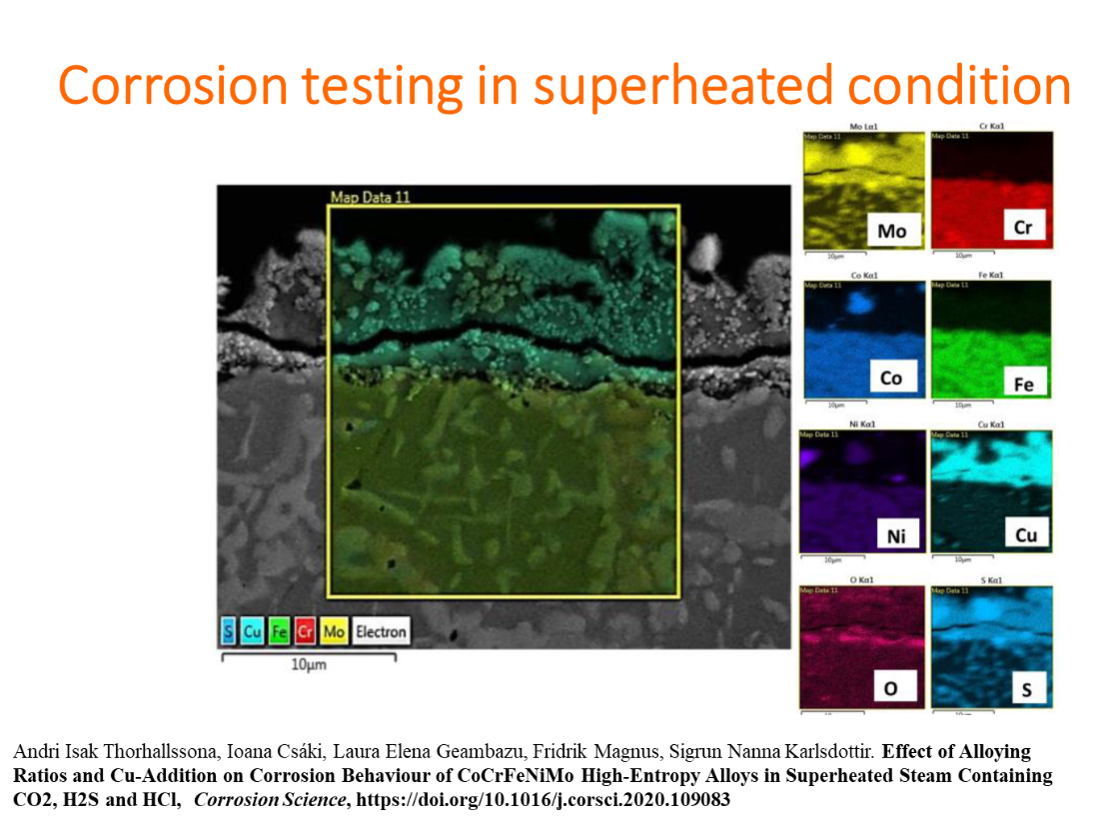
Scanning electron microscopy and mapping with Energy dispersive X-Ray Spectroscopy of the cross-section of a corrosion coupon
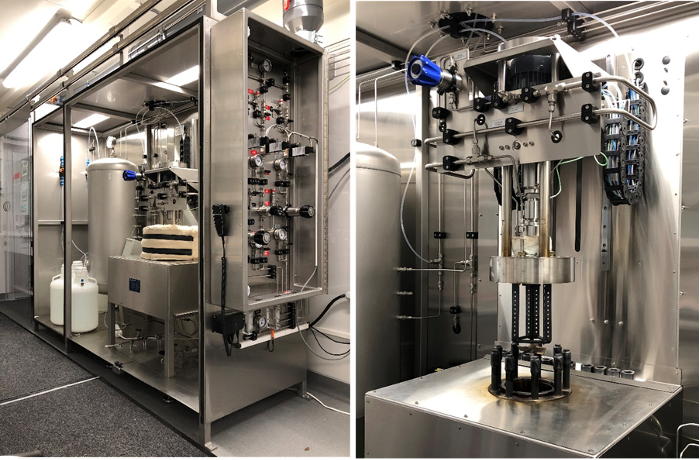
Materials engineering & Corrosion Center geothermal research projects:
GeoDrill
The objective of the project is to develop a novel materials and drilling technology for geothermal systems. Geo-Drill aims to reduce drilling costs through DTH hammer, to advance drill monitoring through low-cost and robust 3D printed sensors and improve component life through advanced materials and coatings. The GeoDrill project started in 2019 and received funding from the European Union’s Horizon 2020 research and innovation programme, Grant agreement no. 815319.
Geo-Coat
The objective of the project, which started in 2018 is to develop novel and cost-effective corrosion-resistant coatings for high-temperature geothermal applications. In this project, various potential corrosion resistant coatings were tested by Prof Karlsdottir’s research group to identify the best coating material for critical parts of the production line in geothermal power production. The coatings were tested in a simulated geothermal environment in a high-temperature corrosion testing facility at the MEC Center, University of Iceland. The project was funded by the European Union’s H2020 research and innovation programme, Grant agreement, no. 764086.
GeoHex
The objective of the GeoHex project is to develop advanced materials with anti-scaling and anti-corrosion properties for cost-efficient and enhanced heat exchanger performance for geothermal applications. The project received funding from the European Union’s Horizon 2020 research and innovation programme in 2019. Grant agreement no. 851917.
Material research & modelling for high temperature & superhot deep geothermal wells
The objective of the project is to investigate the corrosion resistance and high-temperature stability of casing materials in supercritical and superheated steam that resembles conditions in a deep geothermal environment. This will increase the knowledge concerning corrosion behaviour of materials in deep geothermal well environments. In this project, unique High Temperature and High Pressure (HTHP) autoclave corrosion facility located at the MEC Center will be used for simulating the chemistry and conditions of superhot geothermal wells to test selected developed materials. The project is funded by the Icelandic Technology Development Fund, and by the Icelandic Centre for Research (RANNÍS). Time Period: 2021-2024. Grant no. 2113356-0611.
Please note: This is a commercial profile
© 2019. This work is licensed under CC-BY-NC-ND.