Wayne Davies, Energy Markets Programme Manager at Enel X UK, argues that intelligent software is key to unlocking value for CHP plants
Combined heat and power (CHP) plants, or cogeneration, provide a highly efficient way to generate on-site electricity and heat – but add intelligent software to the management process and plant owners and operators can realise opportunities to increase efficiencies and generate new revenue that may have not existed before.
For public sector organisations, improving CHP efficiency helps reduce emissions for those on a journey to net-zero, while additional revenue can be invested in services or new low-carbon projects.
CHP fundamentals
Typically, CHPs consist of a ‘prime mover’; an engine or turbine connected to an alternator to generate baseload electricity, and a heat recovery mechanism to capture heat from the engine that would otherwise go to waste. The heat recovery unit produces hot water or steam that contributes to the site’s thermal needs.
Like most distributed generation plants, power generated for use locally is immune to faults in the larger grid system. This helps to achieve good efficiency and also reduces emissions. But specifying the power output to accurately meet a site’s demands can make further significant improvements to efficiency.
Early adopters of cogeneration include manufacturing sites that operate continuous processes with a need for constant baseload power. Sectors that match this user profile include food, chemical and cement manufacturing. However, university campuses and hospitals also see value in having efficient on-site generation, especially when there is also demand for hot water or heating.
Finance and fuel flexibility
Installing a CHP unit doesn’t necessarily require a capital outlay. Alternative options to finance cogeneration projects include buying the generated power through a power purchase agreement for a fixed term or contracting with an energy service company (ESCO). ESCOs typically offer a range of finance models, including financing through shared energy savings. Some governments also offer tax incentives, which can make the financial case for CHP even more compelling.
Most CHP units operate by combusting fuel or feedstock to create steam in a boiler that drives a turbine, which generates power. The exhaust gases pass through a heat recovery unit to reclaim the heat. Fuel options include gas and carbon-neutral fuels such as biogas from anaerobic digesters, wood chips, agricultural residues and other forms of biomass feedstock. Some CHP manufacturers are now looking at the possibility of using hydrogen as a fuel, which will further improve the low-carbon credentials for on-site baseload generation.
Achieving high efficiency
It is feasible to achieve efficiency levels of 80-90% with modern CHP plants. Typically, supplying a CHP with 100 units of fuel would yield about 35 units of electricity and 45 units of hot water. By comparison, separate engine and heating systems require 148 units of fuel to achieve a similar output of electricity and heat.
While the primary motive for installing a CHP is often to save money on energy bills, it’s not the only benefit. Investing in on-site generation removes exposure to energy market price volatility, making forecasting energy spend more predictable. CHPs also improve resilience for a site by protecting it from exposure to any grid issues, such as blackouts.
The icing on the cake, however, is that in countries like GB, which have a market for real-time grid balancing, CHP operators with flexible capacity can generate revenue by selling spare capacity back to the grid.
Implementing dynamic operating schedules
CHP units that haven’t been optimised to serve variable site loads typically operate at sub-optimal performance. Generating heat and electricity surplus to requirements simply wastes energy, reduces site efficiency and is bad for the environment.
By retrofitting intelligent software controls to optimise the management of a CHP plant, energy managers can improve the utilisation of these assets. Compared with deploying a static operating schedule, controlling the CHP unit dynamically minimises energy waste and maximises the value of flexible capacity. (Figure 1)
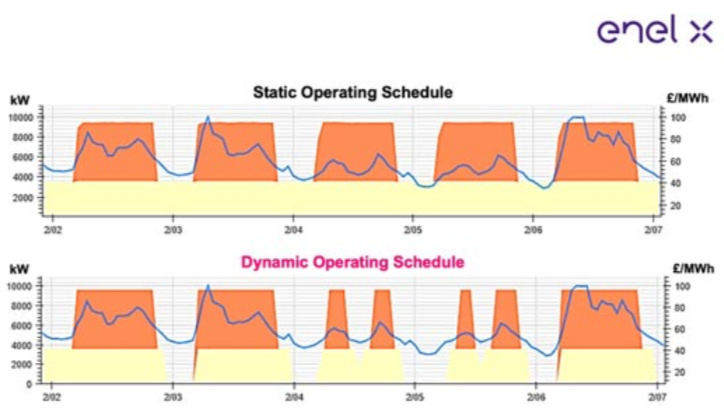
The static schedule shows two CHPs – a 3.6MWe CHP unit in yellow and a 6MWe unit in orange, alongside the power price (blue line). The 3.6MWe CHP operates at 100% output 24×7, while the 6MWe unit operates at 100% during business hours. The dynamic operating schedule shows how the same units would respond to changes in power prices. The 3.6MWe CHP operates at 100% during business hours (8am – 8pm) but reduces output midday on 2/04 and 2/05 reacting to a dip in power price. The 6MWe CHP operates at 100% during business hours but shuts off completely midday 2/04 and 2/05 reacting to the dip in power price.
Optimising flexibility trading
As energy system operators continue to integrate more renewable energy on the grid, they need more flexible capacity to balance supply and demand.
Recently, the GB electricity system has seen several price spikes in both spot energy markets and its balancing mechanism due to variable wind and load profiles. Wholesale power prices peaked at over £500/MWh in early 2021 due to a combination of low temperatures, low wind generation and high demand.
Using intelligent software to combine knowledge of operating parameters with grid signals and market indicators, such as energy market price information, it’s possible to create the best running schedule for the CHP plant. The algorithms can then identify opportunities to trade any flexible capacity in the most appropriate markets.
CHP plants are inherently highly efficient for on-site power and heat generation. By deploying intelligent, dynamic software management technology, operators can increase control and monitoring over the whole CHP system. This enhanced level of visibility provides clarity over site energy costs; helps energy managers to understand and accommodate site and contract constraints; further minimises energy costs by reducing waste and inefficiencies and enables efficient energy trading in flexibility markets.