Adélio Mendes, Full Professor from University of Porto and coordinator of 112CO2 project, describes the concept of low temperature catalytic methane decomposition for COx-free hydrogen production
The world needs a disruptive tech-nology to quickly decarbonise the energy sector; the success of this technology critically depends on its social acceptance, sustainability, low-cost and fast implementation. The 112CO2 team believes to have this technology in place, the so-called methane decomposition is required for the cost-effective production of CO2-free hydrogen.
Methane decomposition for COx-free hydrogen production
Methane decomposition (MD) reaction converts methane from natural gas or biomethane into solid carbon and hydrogen. With the advantage of being 100% selective, this reaction has the power to produce clean hydrogen and remove atmospheric CO2 at competitive costs. The state-of-the-art process for producing hydrogen from MD uses a moving bed reactor loaded with coal pellets, running at ~1400°C. The main objectives within the framework of 112CO2 are to bring the temperature down to 550°C and produce pure hydrogen in a compact, transportable, cheap and stable reactor; low stabilities are an issue at low-temperature processes. The 112CO2 project started in September 2020 and gathers some of the most outstanding EU research laboratories and companies (UPORTO, CSIC, DLR, EPFL, Pixel Voltaic, Paul Wurth, Quantis).
“The main innovations that are being addressed within 112CO2 are: i) making the MD catalyst very active, stable and regenerable; ii) high temperature hydrogen electrochemical pumping and purification; and iii) demonstrate a compact and efficient reactor to be operated at low temperatures.”
MD catalyst development is a cooperative effort by CSIC, UPORTO and EPFL. Nanoscale control over composition and nanostructure is used as a driver towards highly active catalysts, which are additionally amenable to a cyclic regeneration by hydrogenative gasification of a fraction of the deactivating carbon deposits on the active surfaces, with minimum hydrogen use. During the project’s first implementation year, precise catalyst synthesis methods enabled the understanding of fundamental aspects of how this reaction proceeds on metallic nanocrystals, for example, structure sensitivity phenomena. This information has led to the identification of optimal metal nanocrystal sizes that result in very high hydrogen production rates (>3 gram of hydrogen per gram of metal and hour) at remarkably mild operation temperatures (<550°C). In close cooperation with reactor prototyping, further catalyst design research focuses on control over interfacial effects at the nanosized active metals level, with input from computational simulations, to enhance hydrogenative catalyst regeneration to sustain the already high production rates achieved over very long operation times.
Innovation in the field
DLR and UPORTO are working together to develop a device to purify the obtained hydrogen into the reactor. The device should be simple and suitable for being integrated into the reactor, and the process must be energy efficient. Our proposition is an electrochemical hydrogen pumping device based on Proton Conducting Ceramics (PCC). PCCs are promising for electrochemical energy conversion devices, such as fuel cells, steam electrolysers, as well as hydrogen pumps. It can work well at the operation temperature of the reactor, which is ideal since no additional cooling/ heating is required. Moreover, electrochemical pumping can pressurise the hydrogen up to several bars, and no pressurised condition is necessary in the reactor. Based on the successful demonstration of PCC at DLR, metal supported PCCs are being developed for a cost-efficient hydrogen pumping device, using porous metal substrates made of cheap stainless steel to manufacture PCC cells by combining wet-chemical and dry physical processing routes for integration into single pumping units into the reactor.
UPORTO, the inventor of this new MD concept, is developing a new MD reactor approach for this process, allowing cyclic hydrogen regeneration. It is expected to reach >0.45gH2 .g-1cat.h-1 and be stable for >10000h. Carbon production, an added-value by-product, cannot only cover the catalyst surface, but also clog the reactor during operation. Therefore, the reactor design is being optimised for improving the hydrogen production, for easy regeneration of the catalyst and easy removal of the produced carbon flakes. Preliminary results with a commercial, non-optimised catalyst and with cyclic regeneration allowed to maintain the activity during >200h. Pixel Voltaic, a spin-off company from UPORTO, is developing a lab prototype reactor. This demonstrative device, including the MD catalyst and PCC membranes, will be tested under real conditions to push the technology from TRL1 to TRL4.
The life cycle assessment (LCA) of this revolutionary new technology is being addressed at Quantis, following the international standards (ISO 14044), to identify the environmental performance and key drivers of the technology when compared to alternative solutions. Under development competing processes are running the MD reaction at high temperature and namely, they employ metal liquid reactors (~1000°C), iron ore (~900°C) or carbon catalyst (~1400°C). These alternatives, however, are very energy-intensive, dangerous to operate and use a very expensive reactor. The results will provide recommendations on the most promising configurations, thus guiding eco-design choices and sustainable integration of the 112CO2 technology.
Economic assessment
Besides LCA, an economic assessment will be performed for determining the price of the hydrogen produced by MD for various scenarios. Considering only the price of the raw materials, hydrogen from natural gas and biomethane costs €5.2/kg and €5.9/kg (assuming €83.9/MWh for natural gas, €95/MWh for biomethane and €20/MWh for electricity). However, to these values, it should be removed the price of selling the produced carbon (assumed €143/tonne) and, in the case of biomethane, it should be also considered the removal of CO2 from the atmosphere (assumed €88.9/tonne of CO2 removed), which account for €0.43/kg and €1.42/kg, making the final price of hydrogen produced from natural gas to be €4.8/kg and produced from biomethane to be €4.5/kg. At the current price of CO2 allowances (ca. €88.9/tonne), hydrogen from steam reforming of methane costs €5.0/kg (just the cost of methane and CO2 allowances), being more expensive than the MD of natural gas. The produced carbon will be valorized namely for civil engineering, soil amendment, coating roads and electrodes in electrochemical systems.
112CO2 also proposes an ambitious communication strategy, aiming to involve stakeholders, investors, researchers, youngsters, and students for this emergent technology. UPORTO is responsible for the social impact analysis. The mapping of the external stakeholders is currently underway; they were identified by activity sector and classified by four indicators: interest, urgency, risk, and influence.
Visit the 112CO2 website to learn more about the project. The project includes two prizes (~€140k) related to “build-up of an interdisciplinary community” and three grants (~€65k) regarding the creation of an innovative eco-system around MD.
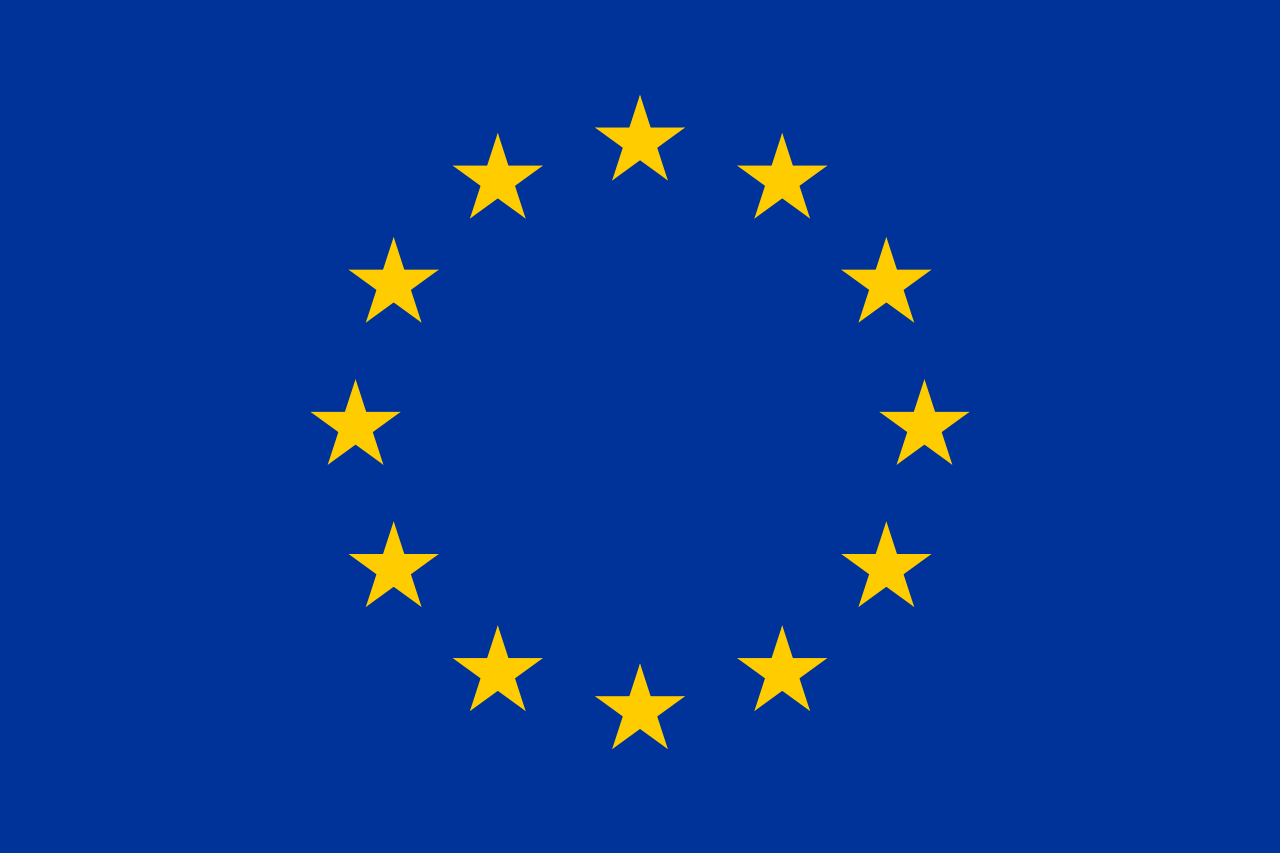
Please note: This is a commercial profile
© 2019. This work is licensed under CC-BY-NC-ND.