By modelling particulate erosion, Dr Louise Crocker of the National Physical Laboratory hopes to improve design and understanding of materials…
The efficiency of high temperature energy generation plant and aero-engines is critically impacted by solid particle erosion, particularly at elevated temperatures. The cause and type of solid particle erosion varies across different industries and locations in plant. In all cases the performance of materials can be improved through better surface engineering and coatings, but this is restricted due to lack of generic models, well-controlled and instrumented tests, and international standards. For industry the long-term aim is to develop a system where the components are manufactured from appropriate materials, the materials degradation modes are identified, and that models exist to predict material performance.
A review in 2010 identified the limited number of high temperature solid particulate erosion (HTSPE) testing facilities worldwide for the measurement of high temperature particulate erosion. Those that exist are limited in terms of the particle velocity and temperature. A European initiative – METROSION – had a primary objective to develop a metrological framework necessary to fully instrument and monitor HTSPE testing. As part of this initiative, the National Physical Laboratory (NPL), the UK’s National Measurement Institute, designed and built a new HTSPE test to extend the capability of high temperature erosion tests, carrying out experiments at temperatures up to 900°C and particle velocities up to 300 ms-1. The novel design approach for the new NPL rig involves the use of a compact air heater. This connects directly to the particulate delivery nozzle providing a simple method for heating gas to any required temperature.
To achieve the necessary performance envelope of the nozzle, an extensive period of design using Finite Element (FE) modelling was conducted by modelling experts within the Materials Division at NPL. To ensure the nozzle would meet the requirements before machining the component, a parametric study was carried out to select the dimensions of the nozzle, balancing the gas flow, gas pressure and nozzle geometry to achieve the design goals. Simulations were conducted for the chosen optimum dimensions, changing the inlet pressures and flow rates within the permissible ranges, to make sure that the target outlet speed of 300 ms-1 was achieved at a temperature of 900°C. Validation analyses were carried out using the same modelling principles to represent an existing nozzle used on a partners HTSPE apparatus; the predictions agreed well with experimental data.
The use of FE modelling has been critical in defining the experimental set-up of the new HTSPE rig by extending the nozzle model to include the sample and air, enabling prediction of the gas plume as it leaves the nozzle and reaches the sample. The effect of parameters such as stand-off distance and impact angle on the gas flow exiting the nozzle and impacting the sample were studied. This modelling showed the influence of impact angle on the vertical and horizontal velocity components, showing that a glancing angle impact, e.g. 30°, generates a large area of stable horizontal velocity.
We know that erosion is a complex process, strongly affected by factors such as shape, size, density and hardness of erosive particles, properties of the substrate/coating, and particle velocity and impact angle. Material degradation is often unavoidable but the ability to model the erosion process allows us to improve design through better material selection and the use of erosion reducing measures. Modelling of the erosion process is invaluable in interpreting existing experimental data, or extending experimental data to conditions that cannot be tested. At NPL we have developed an FE model to simulate material removal through the use of advanced tools such as element failure and deletion. The model simulates a small number of particles impacting a substrate and the subsequent loss of material allowing erosion rates to be calculated directly. In setting up the model, no experimentally determined erosion constants are required. Only the material properties needed for the material model are used, thereby using physics and physical properties to model the materials performance rather than empirically fitted data.
Within the model the impact velocity, angle and locations can be controlled to investigate the effect of subsequent impacts. The method also enables the direct prediction of other outputs such as residual stresses, crater depths, plastic strains and particle velocity and displacement. Our model shows clear trends in the prediction of erosion rate with varying impact angle, along with changes in the particle behaviour – from bouncing off the surface to skimming along the surface – causing more erosion and possible particle embedding. An NPL Good Practice Guide is to be published shortly, giving guidance on the use of FE analysis for predictive erosion modelling.
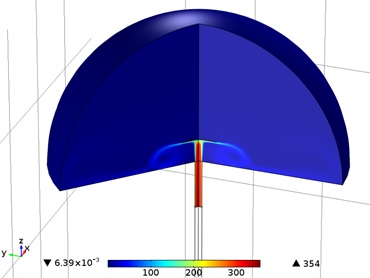
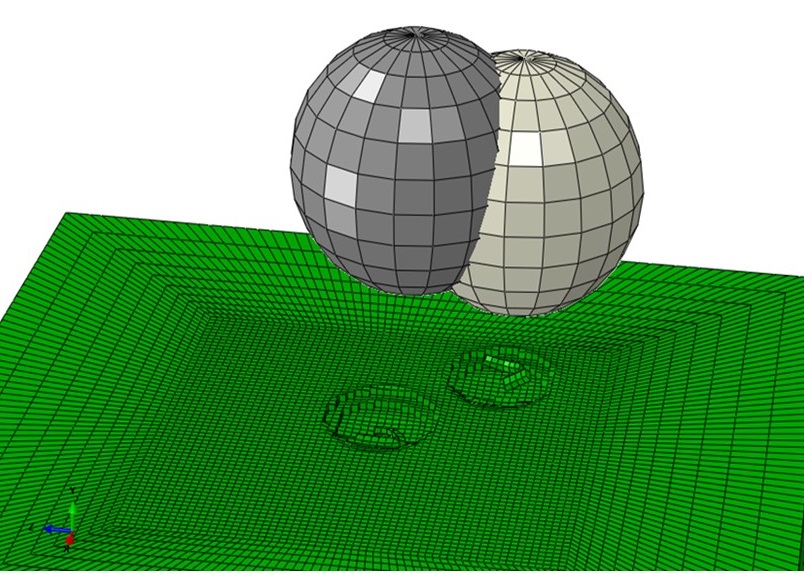
Dr Louise Crocker
Senior Research Scientist
National Physical Laboratory
louise.crocker@npl.co.uk
Please note: this is a commercial profile