Julie Neal, director at management consultancy Vendigital, discusses why private equity firms must re-focus on optimising portfolios
With costs rising due to inflation and warnings of tougher economic conditions, private businesses are entering a period of significant instability. Private equity firms are responding by re-focusing on optimising their portfolios to drive enterprise value.
An uncompromising focus on delivering a healthy return on investment (ROI) has always been a key driver for private equity firms as they look for ways to make their funds stand out to high-net-worth and institutional investors. Facing a prospect of limited or negligible growth in the year ahead, fund managers need to be able to demonstrate that their portfolio businesses can still deliver a robust ROI over a reasonable timeframe.
The ultimate goal for a portfolio company is to create value by improving operating performance and growing the business, thereby increasing its valuation. However, this typically requires significant upfront investment and capital injection to get things underway. Being able to demonstrate a commitment to cost and value engineering best practices could help them to secure the funding needed to further their growth strategy. Equally, pre-private equity businesses know that it may be possible to attract higher multiples from firms on the way in by optimising value creation.
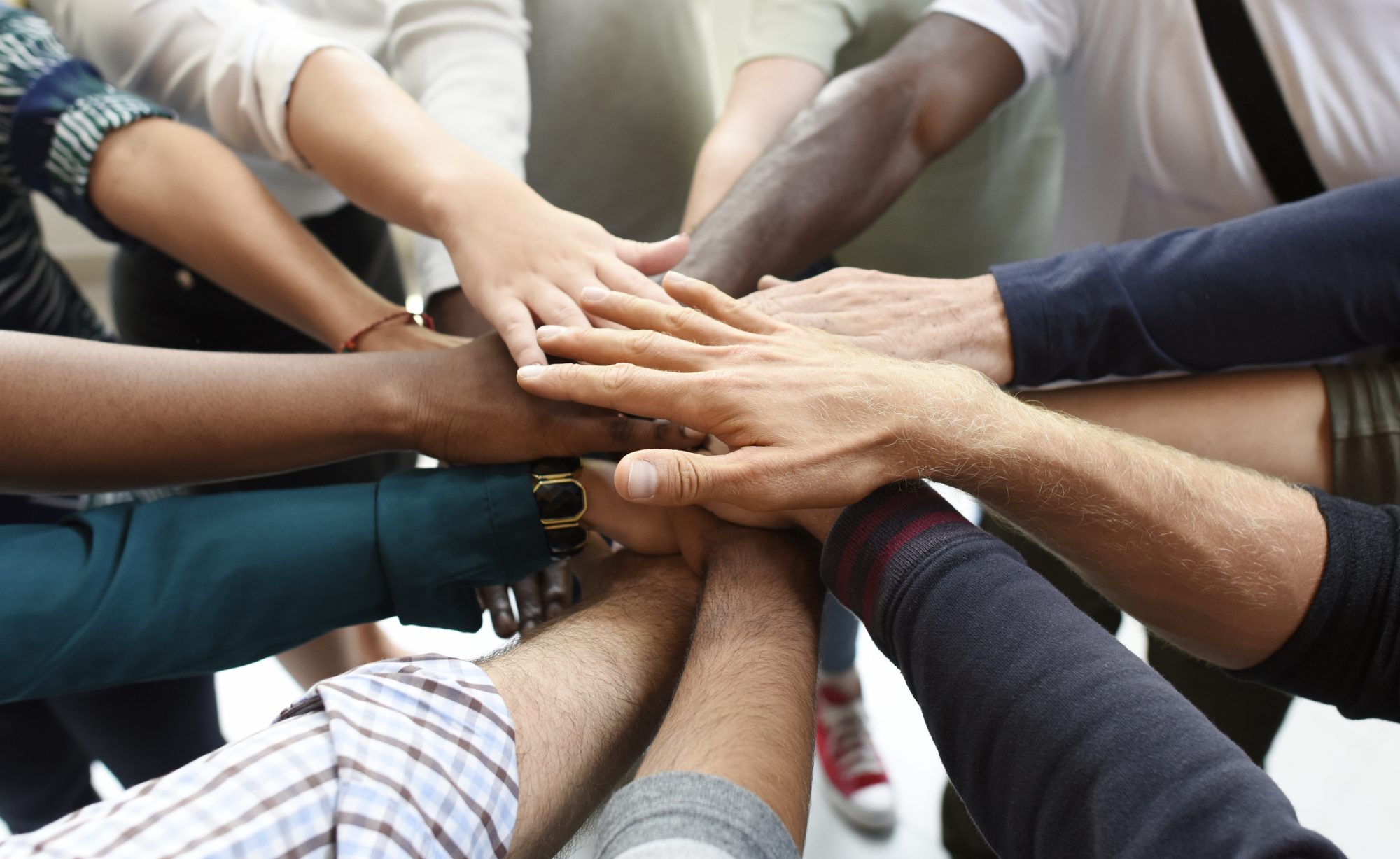
Businesses must ensure they understand what customers want
There are three main areas of focus for operational effectiveness projects, which start by ensuring that the business understands its customers and what they want. Another important consideration when looking for ways to reduce cost and drive value is digital skills and ensuring that decision-makers within the business have access to accurate and reliable data. Finally, operational efficiency should also be examined closely to identify opportunities to improve processes and systems and accelerate the route of the market.
For manufacturing businesses, conducting a ‘make or buy’ analysis based on benchmarked cost data could help to identify efficiencies, some of which can be delivered relatively quickly. It can also help to establish if the business is charging the right price for its product. In a climate of high inflation and significant cost volatility affecting areas such as commodities and transportation, in particular, businesses are finding it more difficult to adapt their pricing models and are unsure how much customers will be able to take. Internal and external data can help to increase visibility and support decision-making in this area.
To ensure their success, cost and value engineering projects should be based on an end-to-end review of management functions, production processes and supply chains. This detailed analysis will help to identify the cost drivers of the business, which can then be assessed further. For example, if a component manufacturer is producing metal parts but also generates a significant amount of scrap metal as a by-product, it may be possible to change manufacturing methods to reduce waste. Alternatively, shift patterns could be altered to increase productivity and minimise machine downtime.
Increased cost visibility will help to improve the management team’s understanding of how costs translate into revenue to optimise operational efficiency. The business should aim to understand how much it costs to produce £10 of revenue, so it can be sure that profitability ratios are being met. By building dynamic cost models, the business can enter scenario-based cost increases and see the impact on the bottom line over a three-month timeline. Based on these cost models, private equity-backed businesses can prepare for a period of sustained high inflation by making efficiencies and strengthening relationships with customers and suppliers as they do so.
Written by Julie Neal, a Director who specialises in advising private equity firms and private equity-backed businesses at management consultancy, Vendigital