Ying-Chieh Lee from the Department of Materials Engineering, National Pingtung University of Science and Technology, explores the development of a renewable product prepared using economic waste in Taiwan
Today, increasing reliance on natural resources and the effects that particular economic growth trends have on the ecosystem are becoming critical, and have significant social consequences. Since large-scale coal firing for power generation started in the 1920s, several million tonnes of ash and related by-products were produced. The global annual output of coal ash worldwide is projected to be around 600 million tonnes, with fly ash accounting for around 500 million tonnes at 75–80% of the total ash produced (1). Fly ash, generated during the combustion of coal for energy production, is an industrial by-product that is recognised as an environmental pollutant. Because fly ash is an environmental problem, considerable research has been undertaken on the subject worldwide. In Taiwan, more than 5 million tonnes of fly ash have been produced annually from coal combustion in power plants. During the 20 years of statistics, the fly ash of Taiwan power company increased to about six times. However, the utilisation rate of fly ash has tended to decrease during recent years (for example, from 95.1% in 2004 to 49.4% in 2009) (2). The wet disposal of increasing amounts of unused fly ash into ash ponds has gradually become one of Taiwan’s major environmental problems. The current recycling methods cannot accommodate a large amount of coal-fired fly ash and meet its recycling demand.
Renewable plastic composite for agriculture application
To synthesise the renewable feldspar (CaAl2Si2O7) from coal-fired fly ash and oyster shells, which can obtain the powder characteristics, such as pale yellow, below 10 μm particle size, 5~6 Mohs hardness, < 2.4 g/cm3 density, ~1200 °C melting point (Figure 1). It is very similar to the natural mineral calcium feldspar, and the application is diversified. The renewable feldspar can be applied in industries such as plastic fillers, rubber filler, coatings filler, and building materials. This new recycling technology addresses issues with large amounts of fly ash and eliminates the massive amounts of contaminated oyster shells that threaten the ecosystem and ecosystems. In this sense, this Special Topic aims to take a broad viewpoint on the relations between economic structures and climate. Using this technology, feldspar paper, heavy metal adsorbent, garbage bags, tote bags, and other products were successfully produced with renewable feldspar powders (Figure 2).
Renewable plastic composites from industrial waste
Instead of fly ash, plastic pollution has become one of the most pressing environmental issues, as rapidly increasing production of disposable plastic products overwhelms the world’s ability to deal with them. Taiwan also produces more than 35,000 tonnes/year of PET, nylon, and glass fibre reinforced nylon waste. Plastic products have also been recycled into many recycled products recently to promote environmental protection. Based on the plastic recycled materials, our research has been successfully developed so that the renewable plastic composite materials can be applied in an agricultural greenhouse and as a material to support the growth of woodbine plants (Figure 3). This composite support can replace galvanised steel pipes as the main material usually used in the greenhouse with lightweight, simple, not easy to corrode, and low-cost fabric that is more often adopted by general farmers. This type of greenhouse can achieve the concepts of “reducing material costs” and “green materials” for recycling, protecting the environment as the priority, and creating new agricultural economic energy development.
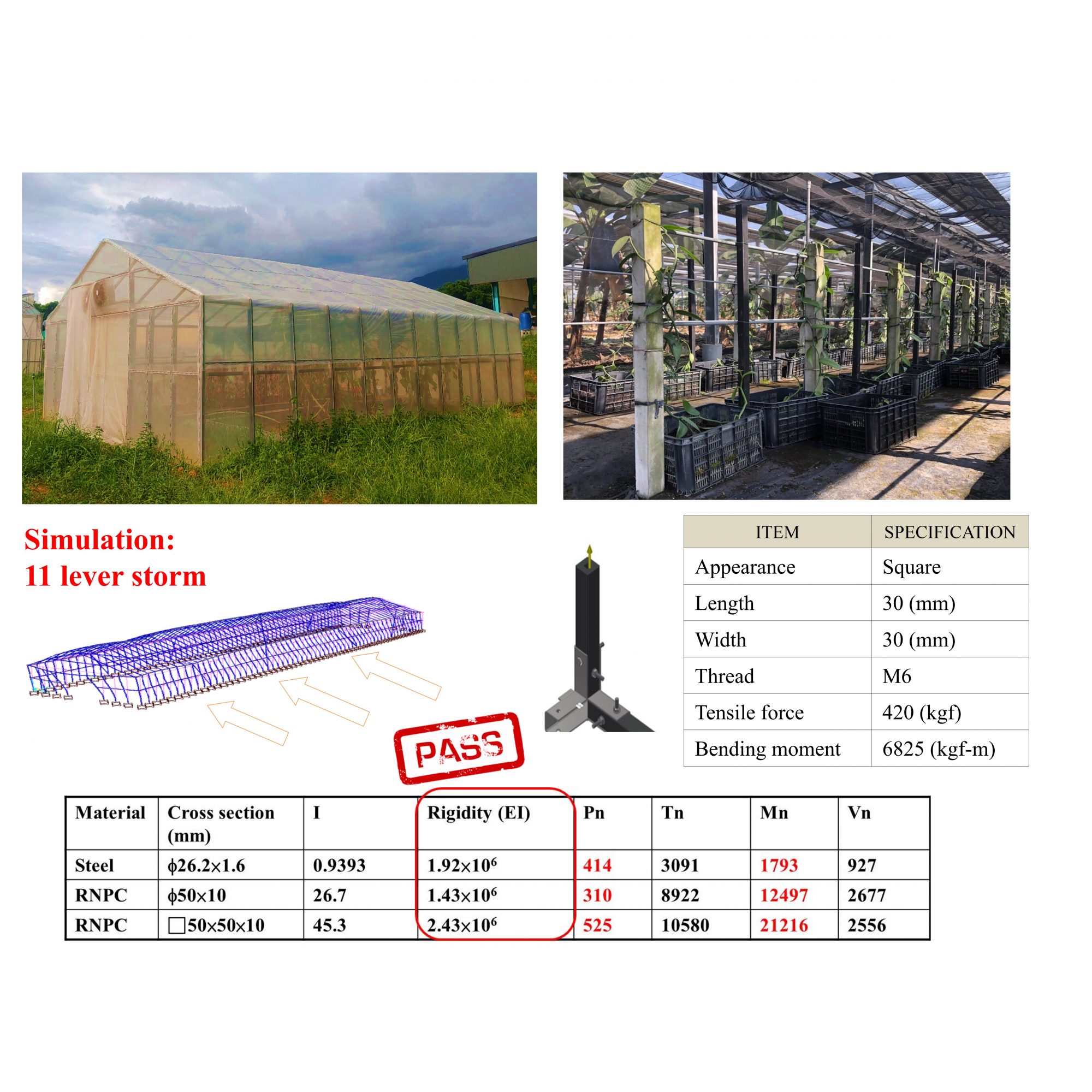
Producing ceramic composites from industrial waste
On the other hand, we are also concerned about producing ceramic composites from industrial waste. Solar energy is strongly favoured over fossil fuels by many kinds of renewable energy. However, waste-cutting oil is generated during solar panel production. Cutting oil includes silicon, silicon oxide and diethylene glycol (DEG) in silicon mud. Reusing the cutting oil as reusable products would minimise waste oil disposal prices, reducing the environmental effects of waste cutting oil. Silicon carbide (SiC) has been widely studied due to its unique properties, such as high hardness, high strength, low thermal expansion, high thermal conductivity, and excellent chemical stability at high temperatures. SiC also has better bending strength than other ceramic materials at high temperatures. It is a semiconductor and is often used in high-temperature electronics. We have developed SiC ceramic substrates prepared with 99.5% silicon carbide powders, which came from waste silicon mud during the solar cells’ manufacturing process. We found that SiC powders with SiO2 addition show the most optimum outcome with more robust mechanical properties. This study result could be a successful and potential substitute for materials. We are concerned about reducing costs and producing products with attractive properties. Looking ahead, our future research sets out to pursue more waste products and possible technologies, turning waste into environmentally sustainable and high economic potential renewables.
References
(1) Ahmaruzzaman, M. (2010). A review on the utilization of fly ash. Progress in energy and combustion science, 36(3), 327-363.
(2) Taiwan Power Company, Ltd. Available online: http://www.taipower.com.tw (accessed on 18 November 2020).
Please note: This is a commercial profile