Principal Research Scientist Tony Fry discusses using in situ measurements to accelerate the development of material solutions to particulate erosion
The efficiency of high temperature energy generation plant and aero-engines is of critical importance to OEM (original equipment manufacturer) and operators with impact on desirability and operating costs. The efficiency of plant, whether land based or on the wing deteriorates with use and service life. One of the causes of this gradual deterioration is through wear of leading edges in rotating turbo machinery caused by solid particulate erosion at elevated temperatures. This damage process can reduce the efficiency of turbines by as much as 7 to 10%, and in the case of a large power plant, can cause an additional emission of 250,000 tonnes of CO2 over the lifetime of the plant1. The cause and type of solid particle erosion varies across different industries and locations in plant, for instance the particles could be volcanic ash in aero-engines, fly ash in boilers, exfoliated scale in steam turbines or mineral matter in oil excavation. In all cases the performance of materials can be improved through better surface engineering and coatings, but the development of these is often restricted due to the lack of generic models, well controlled and instrumented tests and international standards.
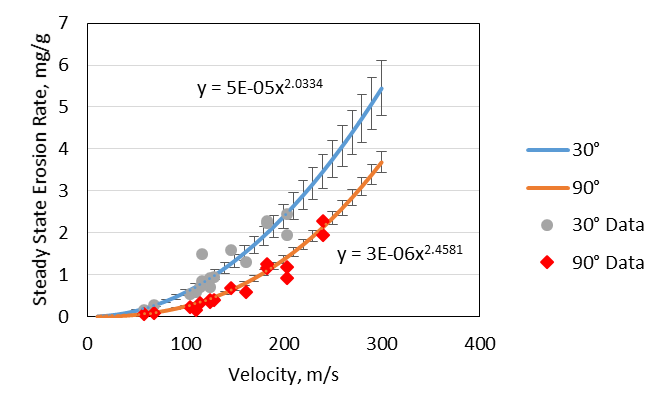
New test facility
The National Physical Laboratory (NPL) in Teddington has been working with other national measurement institutes and research bodies across Europe, to design and build a new test facility. The aim of this being to produce a versatile apparatus with embedded instrumentation to monitor and control the temperature of the gas, sample and particles, to measure and control the gas velocity and to measure the mass change and erosion scar volume in situ during the test. Critically this new test facility includes in situ evaluation of the mass and volume change of the sample and provides a real time measurement of the erosion process, with the added benefit of removing the need to thermally cycle the sample for the ex situ mass and surface measurements at room temperature. This enables the erosion test to be conducted without interruption, thereby allowing the test to be completed in a matter of hours, as opposed to a number of days. This new system has been designed to carry out experiments at temperatures up to 900°C and particle velocities up to 300 ms-1.
To validate the in situ mass measurement against conventional ex situ measurements a small inter-comparison exercise was conducted as part of the METROSION project2. Results from tests performed on Nimonic 80A by the 3 participating laboratories at 600°C using different stand-off distances and acceleration lengths are shown in Figure 1, which presents data collected at 2 incident angles over a range of particle velocities. The error bars represent the standard deviation in the data provided by the 3 laboratories. This shows that the erosion rate from the 3 laboratories fall on the same curve for the different test conditions, providing confidence in the data generated from the in situ measurements compared to the ex situ measurements which were conventionally made. This figure also illustrates the influence of the incident angle on the erosion rate, where the erosion rate is lower at the higher incident angle.
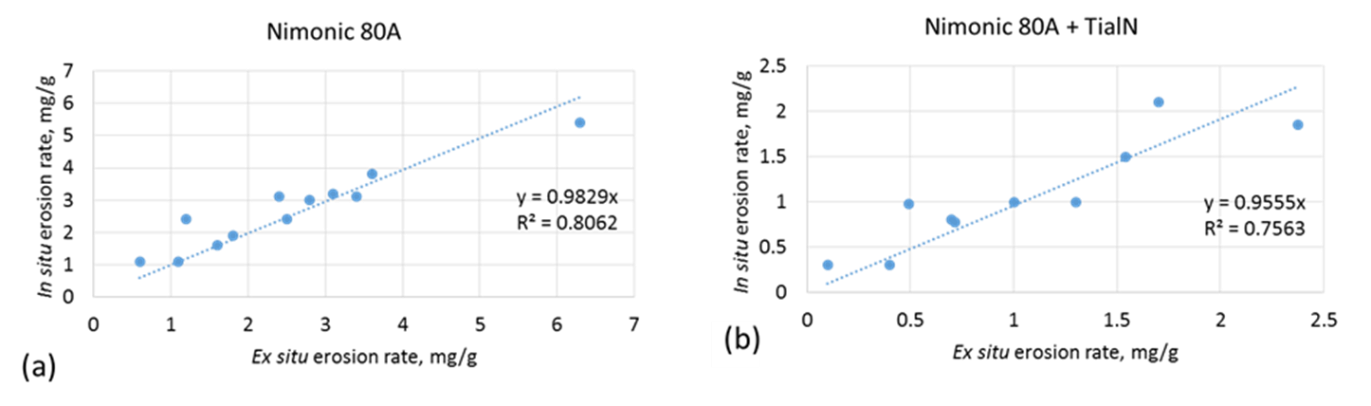
Further tests have been conducted to measure the erosion performance for a range of hard coatings. In each case HTSPE tests were performed at 600°C using 2 velocities of 117 and 140 ms-1 with a stand-off distance of 50mm and incident angles of 30º and 90°. In situ mass measurements were made during the testing. Ex situ data were also obtained after the completion of the tests. Figure 2 shows typical results for uncoated Nimonic 80A and for samples coated with TiAlN, plotting the erosion rates obtained from in situ mass measurements, compared to those calculated from the ex situ mass measurements. For both sets of samples, the slope of the line is close to one indicating that the in situ and ex situ mass measurements agree.
In the uncoated sample, the maximum erosion rate was approximately 6mg/g. The application of a TiAlN coating to the Nimonic 80A substrate has provided protection against HTSPE, reducing the maximum erosion rate to approximately 2mg/g.
It has been demonstrated that this new mass measurement method works well and that it has many benefits over conventional methods. Not only does this new approach allow for the real time evaluation of the erosion rate during testing but it avoids additional errors from thermally cycling the sample and errors in repositioning the sample during room temperature ex situ mass measurements. This approach has the added benefit of decreasing the time needed to conduct a test, from several days to 90 minutes, which in material development provides time and cost savings.
This new erosion test facility adds to the range of tribological measurements NPL can offer industry in the assessment and measurement of material performance. For further information about this EURAMET project, or the range of surface engineering tests and characterisation methods available please contact the Advanced Materials Characterisation group at NPL.
1 K. J. Stein, B. S. Schorr and A. R. Marder, “Erosion of thermal spray MCr-Cr-C cermet coatings,” Wear, vol. 224, pp. 153-159, 1999.
2 Influence of Apparatus Design and Test Method on the High
Temperature Solid Particle Erosion of Nimonic 80A. Fry, A T, et al. Albufeira, Portugal : s.n., 2016. Advance in Materials Technology for Fossil Power Plants.
Tony Fry
Principal Research Scientist
National Physical Laboratory
tony.fry@npl.co.uk
Please note: this is a commercial profile