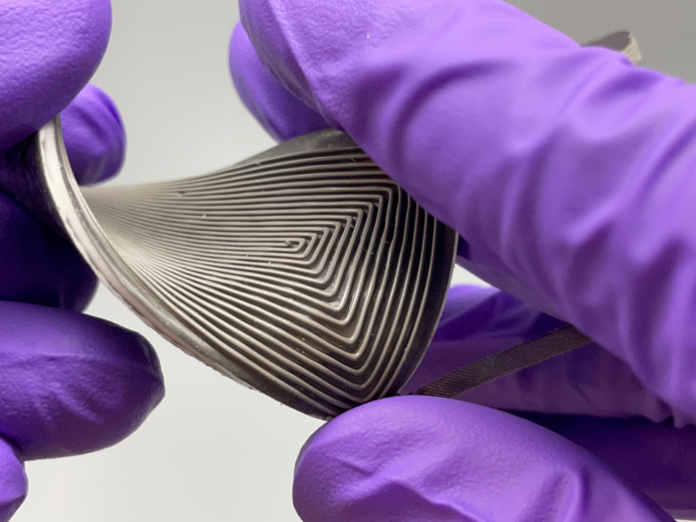
A newly developed thermal energy device presents a new way to continuously power wearable electronics, with a 6.5 times increase in power density compared with other generators
Wearable electronics, from health and fitness trackers to virtual reality headsets, are part of our everyday lives, but finding ways to continuously power these devices is a challenge.
Thermoelectric generators are generally best for stationary conditions as they can continuously harvest thermal energy that would otherwise be wasted to the surroundings due to a heat flux, like a person’s baseline metabolic activity.
One promising solution presented by researchers at the University of Washington is the use of thermoelectric generators which convert body heat to electricity through thermal energy devices.
A highly desirable feature for wearable electronics and soft robotics
To create these flexible devices, the researchers 3D printed composites with engineered functional and structural properties at each layer. The filler material contained liquid metal alloys, which provide high electrical and thermal conductivity.
The researchers’ thermal energy device prototype remains fully functional, even after more than 15,000 stretching cycles at 30% strain, entailing a highly desirable feature for wearable electronics and soft robotics.
The device also shows a 6.5 times increase in power density compared to previous stretchable thermoelectric generators.
What is soft robotics?
Soft robotics is the fabrication of robots composed of compliant materials, instead of rigid links. It focuses on the construction of robots with physically flexible bodies and electronics.
These alloys address limitations in previous devices, including an inability to stretch, inefficient heat transfer and a complex fabrication process.
The team also embedded hollow microspheres to direct the heat to the semiconductors at the core layer and reduce the weight of the device.
Future devices could be applied to clothing and other objects
They printed these devices on stretchable textile fabrics and curved surfaces, which leads the way for for future devices to be applied to clothing and other objects.
Mohammad Malakooti, a UW assistant professor of mechanical engineering, said: “It’s a 100% gain if we harvest thermal energy that would otherwise be wasted to the surroundings. Because we want to use that energy for self-powered electronics, a higher power density is needed.
“We leverage additive manufacturing to fabricate stretchable electronics, increase their efficiency and enable their seamless integration into wearables while answering fundamental research questions.
“One unique aspect of our research is that it covers the whole spectrum, all the way from material synthesis to device fabrication and characterization. This gives us the freedom to design new materials, engineer every step in the process and be creative.”
The team published these findings in Advanced Energy Materials.