Dr Carlos Ziebert at IAM-AWP’s Calorimeter Center of KIT outlines how research and testing in calorimeters is essential to improve the thermal management and safety of batteries
Established in 2011, the Calorimeter Center at the Karlsruhe Institute of Technology’s (KIT) Institute for Applied Materials – Applied Materials Physics, operates Europe’s largest battery calorimeter laboratory. It provides six Accelerating Rate Calorimeters (ARCs) of different sizes – from coin to large pouch or prismatic automotive format – which allow the evaluation of thermodynamic, thermal and safety data for Lithium-ion and post-Lithium batteries on material, cell and pack level under quasiadiabatic and isoperibolic environments for both normal and abuse conditions (thermal, electrical, mechanical).
In addition, the Calorimeter Center contains differential scanning calorimeters (DSC), thermogravimetric analyzers (TGA), laser flash analysers (LFA) and extremely sensible Tian-Calvet calorimeters which provide thermodynamic parameters, such as heat capacity, thermal conductivity or formation enthalpy on the materials level. With these facilities and the established technical and methodological expertise in place, the IAM-AWP is now – seen worldwide – one of the few institutions that investigates both the thermodynamics and the safety of batteries and their materials.
Safety comes first
Safety comes first – this is the mission of the Center’s head, Dr Carlos Ziebert. For a breakthrough of the electrification of transport and for the energy transition using stationary electrochemical storage, the safety of the Lithium-ion cells is one of the most important prerequisites, because an uncontrollable temperature increase (so-called thermal runaway) can cause ignition or even explosion of the battery with simultaneous release of toxic gases.
Thermal runaway is, of course, something that nobody wants, especially in an electric car or another electric vehicle and its causes and effects can be very diverse and complex. Thus, it is fundamental to investigate the thermal effects in close connection with the material and cell development for advanced and post-Lithium systems.
Looking at the current state of the Li-ion technology, we know that the range of properties is still significantly dependent on the respective operating and ambient conditions present. The influence of ageing on safety is another critical factor for commercial applications today. Even the regular use of batteries leads to heat release which makes good thermal management necessary. The heat effects are caused by electrochemical reactions, phase transformations, mixing and Joule heating processes. The active materials can initiate highly exothermic reactions by an internal or external short circuit or by mechanical actions induced by accidents, which can be followed by the thermal runaway. To avoid this, the system must be designed optimally with respect to the material and cell level. In addition, both the battery and thermal management systems must be optimised. Therefore, the complete scientific and technical understanding of the thermal effects is of the utmost importance.
The benefits of battery calorimetry
Calorimetry – or the process of measuring heat data during chemical reactions – allows the collection of quantitative data required for optimum battery performance and safety. This data is important because you need to know how many watts a cell will produce under certain conditions. These data are essential for battery management, thermal management and safety system design. Combined with multiscale electrochemical-thermal modelling, they provide a powerful tool for thermal runaway prevention and ageing prediction.
Sophisticated battery calorimetry combined with thermography allows finding new and quantitative correlations between different critical safety and thermally related parameters. The temperature, heat and internal pressure evolution can be studied while operating cells under conditions of normal use, abuse or accidents. Such abuse tests without a calorimeter have two main disadvantages:
- The maximum safe temperature is underestimated (i.e. the cell would be perceived to be less hazardous) and;
- The thermal runaway consequences would be understated in terms of severity and speed.
- Moreover, a test in the calorimeter is much more sensitive than a hotbox test and reveals the entire process of the thermal runaway along with the different stages of exothermic reactions.
Measurement of thermal data
Fig.1 shows two of the Accelerating Rate Calorimeters (ARC) at the IAM-AWP Calorimeter Center. The cell is inserted into the calorimeter chamber, which has heaters and thermocouples located in the lid, bottom and side wall. These adjust the required ambient conditions, which can be either isoperibolic or quasiadiabatic. Under isoperibolic conditions, the temperature of the calorimeter chamber is kept constant and the temperature change at the surface of the cell is measured. This reflects the ideal conditions of a single cell or an edge cell in the pack. In this case, the cell temperature reaches its initial temperature again after each cycle (s. Fig. 2). In the quasiadiabatic mode the heaters in the calorimeter chamber follow immediately any change of the cell temperature preventing the heat transfer to the chamber. This simulates ambient conditions for a cell in a pack, where the densely packed neighbouring cells greatly reduce the heat release to the environment and leads to a continuous increase of the cell temperature with every cycle, as can be seen in Fig. 3. Such data make it possible to optimise continuously charge and discharge management and to analyse ageing processes in the cells. By measuring the specific heat capacity and the heat transfer coefficient the measured temperature data can be directly converted into generated and dissipated heat data (s. Fig.2), which are needed for the adjustment of the thermal management systems.
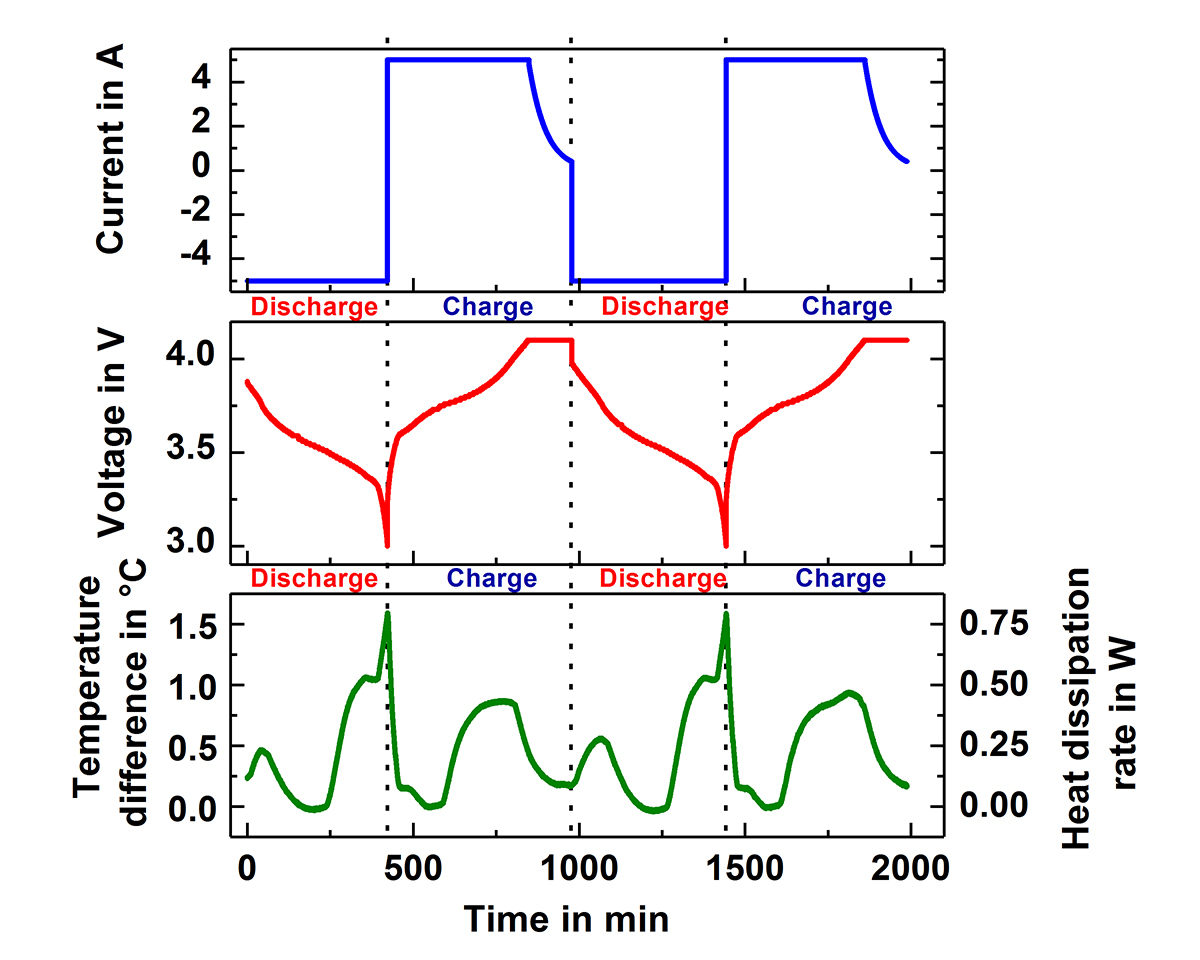
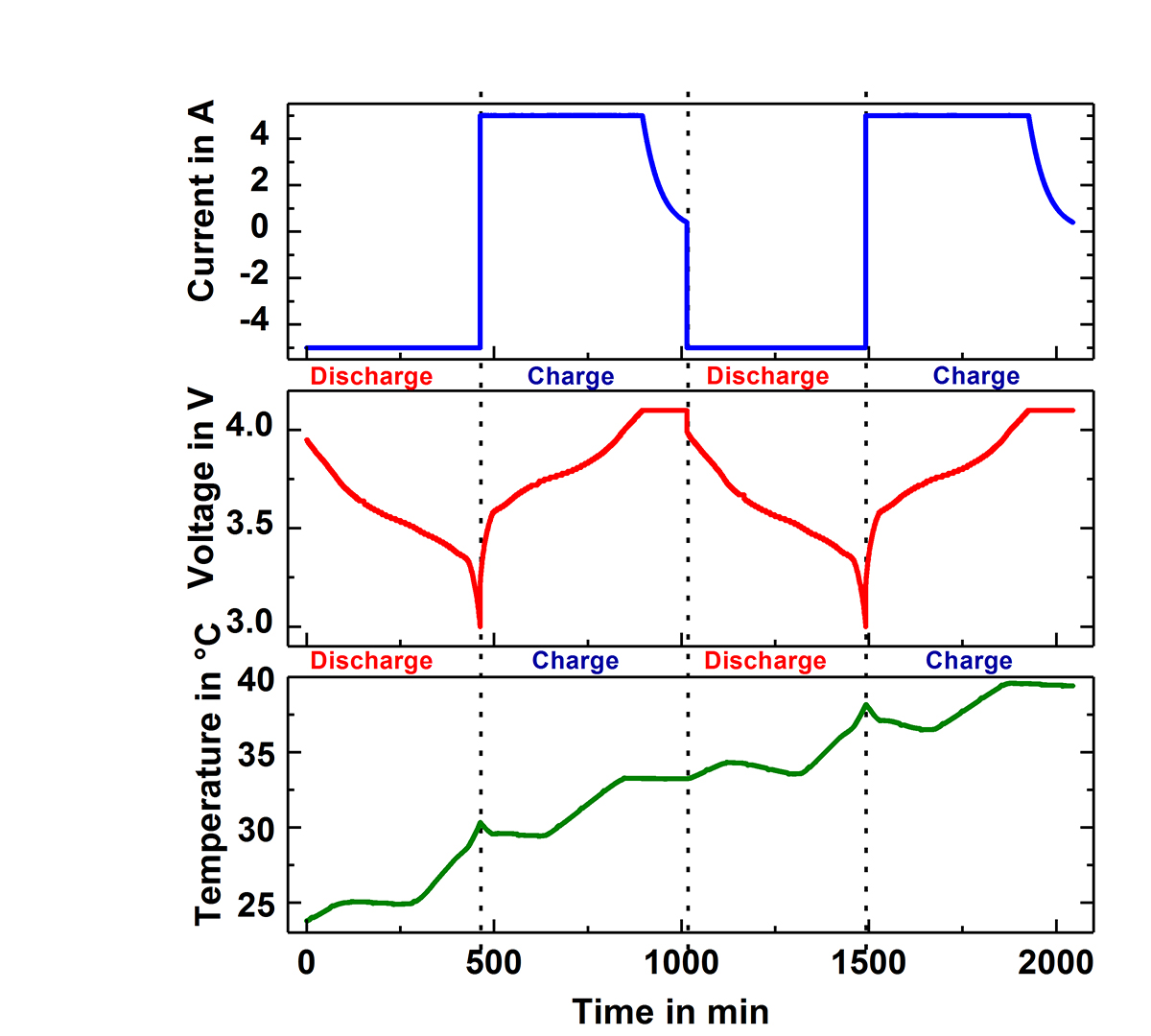
Safety testing
Apart from thermal data under regular use the battery calorimeters provide thermal stability data on materials level, e.g. of anodes, cathodes or electrolytes or their combinations and safety tests on cell and pack level by applying:
- Electrical abuse: External/internal short circuit test, overcharge test, overdischarge test;
- Mechanical abuse: Nail test and;
- Thermal abuse: Heat-Wait-Seek test, ramp heating test, thermal propagation test.
As a result of the different tests quantitative and system relevant data for temperature, heat and pressure development of materials and cells are provided. Currently, the thermal propagation testing is becoming a very hot topic, because a standardised procedure is needed to develop and qualify suitable countermeasures, such as heat protection barriers. For example, a global technical regulation (GTR) on electric vehicle safety is being developed by all relevant stakeholders.
In the future, battery calorimetry will be also needed to assess the thermal and safety properties of advanced materials such as solid state batteries or other systems, which could replace Lithium such as sodium or magnesium. This has to be started already now on the smaller scale level and to be continued to ensure that the cells can be up-scaled and remain safe. Does there are still enough challenges that have to be overcome and we hope that the Calorimeter Center will help the European Industry to make further progress in the battery field, which is urgently needed to reach a low-carbon future, to foster European leadership and to create new jobs.
Please note: this is a commercial profile
Dr Carlos Ziebert
Head of the Calorimeter Center
Karlsruhe Institute of Technology,
Institute for Applied Materials – Applied
Materials Physics
Tel: +49 721 608 22919