Dr Carlos Ziebert, Head of IAM-AWP’s Calorimeter Center, KIT, outlines how research and testing in battery calorimeters improves materials for thermal propagation mitigation in Lithium-ion batteries
It is clear that safety issues have a major influence on consumers’ willingness to adopt Lithium-ion batteries because an uncontrollable increase in temperature of the entire system (so-called thermal runaway) can cause an ignition or even explosion of the battery with the simultaneous release of toxic gases. The causes and effects of this can be very diverse and complex (see Fig. 1). Either internal or external mechanical, operating or thermal stresses lead to internal heating of the cell that initiates different exothermal reactions, followed by further temperature and pressure increases. Cell designs, component integrity, manufacturing and ageing processes all have a critical influence on safety. Currently, a three-level strategy is adopted in order to mitigate the hazard of thermal runaway. The first level is the Battery Management System (BMS), which should be able to detect thermal, electrical or mechanical abuse. The next level is the cell-intrinsic safety features, such as safety vent or current interrupt device (CID).
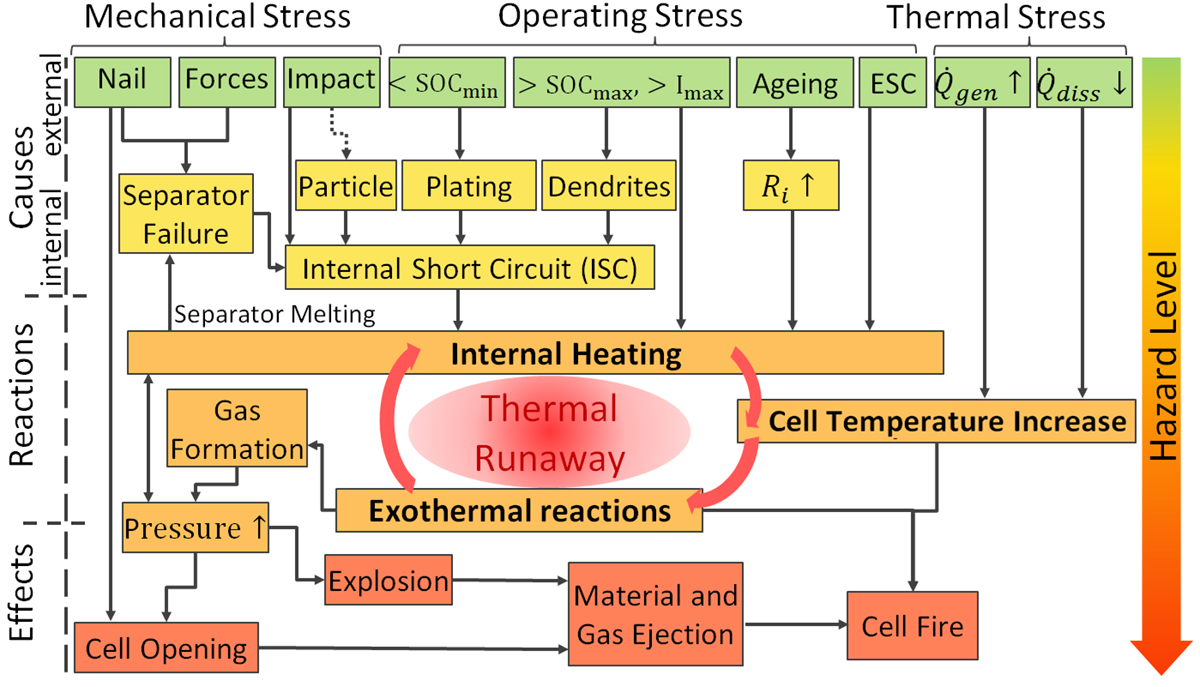
Finally, if it is not possible to stop a single cell from going into the thermal runaway, the last step is to prevent the propagation of the thermal runaway from one cell to the neighbouring cells, the so-called thermal propagation or at least extend the time until thermal propagation to five to 10 minutes. This should give the passengers in an electric vehicle enough time to escape or to be rescued by the firefighters.
Accelerating Rate Calorimeters (ARCs)
Recently at the Calorimeter Center at the Karlsruhe Institute of Technology’s (KIT) Institute for Applied Materials – Applied Materials Physics, a setup was developed, which allows to develop and qualify suitable countermeasures, such as heat shields. This centre, which was established in 2011, operates Europe’s largest battery calorimeter laboratory. It provides six Accelerating Rate Calorimeters (ARCs) of different sizes – from coin to large pouch or prismatic automotive format – which allow the evaluation of thermodynamic, thermal and safety data for Lithium-ion cells on material, cell and pack level for both normal and abuse conditions (thermal, electrical, mechanical). The large-scale ARC’s are well suited for studying thermal propagation.
Single-cell thermal runaway
For such tests, the single-cell thermal runaway can be initiated either by external or internal methods. The internal methods include incorporation of particles and pressing, incorporation of metals with low melting points or incorporation of dedicated internal short circuit devices, like the ISC, which was jointly developed by the National Aeronautics and Space Administration (NASA) and the National Renewable Energy Laboratory (NREL) and recently commercialised by KULR Technology Group Inc. The external methods encompass crush, nail penetration, excess heating, overcharging or external short circuit. They all have different advantages and disadvantages and differ in the amount of excess energy that is given to the cell and the repeatability and reproducibility.
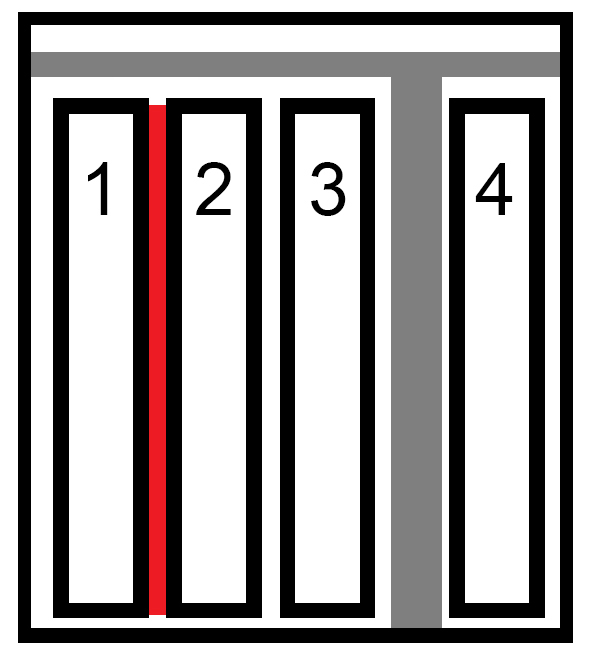
Calorimeter Center
The setup at the Calorimeter Center consists of a metal box, which mimics a battery box and is put into the calorimeter chamber. Four pouch cells are installed in the box and equipped with thermocouples that are connected to the ARC software. A heater mat is attached to cell 2 and the heat shield material to be tested is installed between cells 3 and 4 and below the lid (s. Fig. 2). With the help of the heater mat, cell 2 is now heated up to initiate its thermal runaway. Fig. 3 clearly shows that the thermal runaway is instantaneously propagating to cell 1 and cell 3.
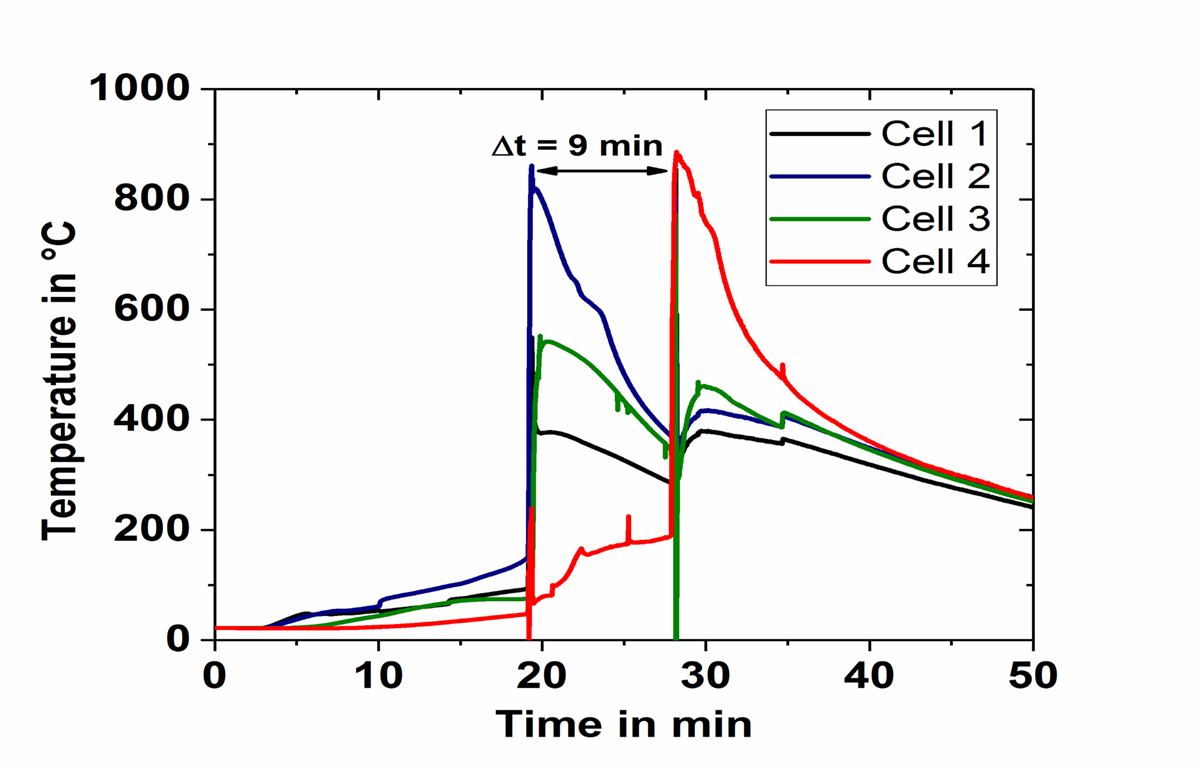
However, the improved protection material DEFENSOR MULTIFLEX® from HKO Group, which was tested in this example, can delay the thermal propagation to cell 4 by nine minutes. In addition, the temperature on the top of the lid, the so-called cold side temperature, stayed below 80 °C during the whole test, whereas temperatures of up to 850 °C were reached inside the battery box.
Currently, a global technical regulation (GTR) on electric vehicle safety is being developed by all relevant stakeholders, which includes thermal propagation. Thus, there are still lots of discussion taking place and ongoing research needed to decide which is the best initialisation method, which could become a standard. We hope that the research in the Calorimeter Center will help to make progress in this field.
Please note: This is a commercial profile